Why clean pellets are essential for every plastic manufacturer
Why Clean Pellets (Free from Dust and Streamers)
Are Essential for Every Plastic Manufacturing Company
Plastic pellets are the lifeblood of the polymer manufacturing industry, serving as the raw material for countless products. However, not all pellets are created equal. For companies aiming to maximize quality, efficiency, and sustainability, ensuring pellets are clean, dust-free, and devoid of streamers is non-negotiable.
In a fast-growing world in the manufacturing sector, maintaining the purity of raw materials like plastic pellets and granular products is critical to meeting global quality standards. Contaminants such as dust, streamers, and foreign particles have long plagued production lines, leading to defects, waste, and compliance risks.
Below, we break down on why this matters and how it impacts every facet of production.

1. Enhanced Product Quality
Contaminants like dust and streamers (thin, hair-like plastic strands) directly compromise product integrity.
- Surface Defects: Dust particles can create pitting, bubbles, or uneven textures in finished products.
- Structural Weakness: Streamers disrupt polymer flow during molding, leading to weak spots or fractures.
- Aesthetic Flaws: Impurities cause discoloration or visible imperfections, reducing marketability.
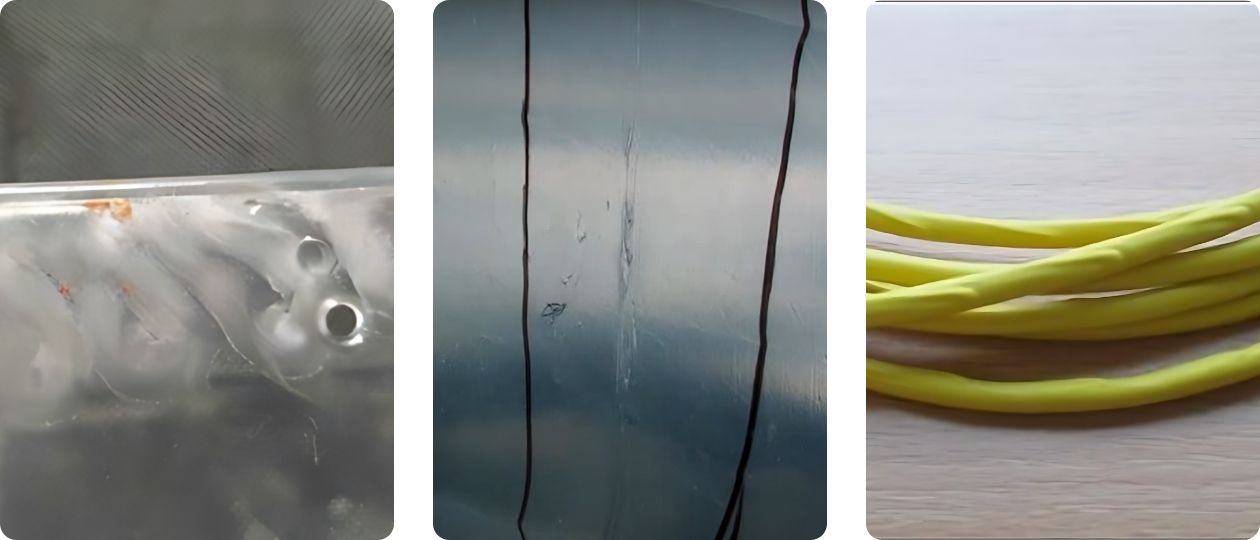
Clean pellets ensure uniformity, enabling precise control over melting, molding, and extrusion processes.
How Dust and Streamers Directly Compromise Product Quality
1. Surface Defects: The Visible Consequences
Dust Particles:
- Act as foreign bodies during melting, creating tiny pits, bubbles, or craters on the surface of molded parts.
- Cause uneven gloss or matte finishes, especially in products requiring high visual appeal (e.g., consumer electronics, automotive interiors).
Streamers:
- Create streaks or weld lines in finished products due to uneven polymer flow during injection molding.
- Leave hair-thin ridges or grooves, making surfaces feel rough or uneven.
2. Structural Weakness: Hidden Risks
Dust-Induced Stress Points:
- Dust particles act as nucleation sites, creating micro-cracks that weaken the product under stress
- Reduce tensile strength and impact resistance, leading to premature failures.
Streamers and Polymer Flow:
- Streamers disrupt the homogeneous flow of molten plastic, causing incomplete filling of molds.
- Result in weak zones prone to fractures, particularly in thin-walled products like packaging or medical devices.
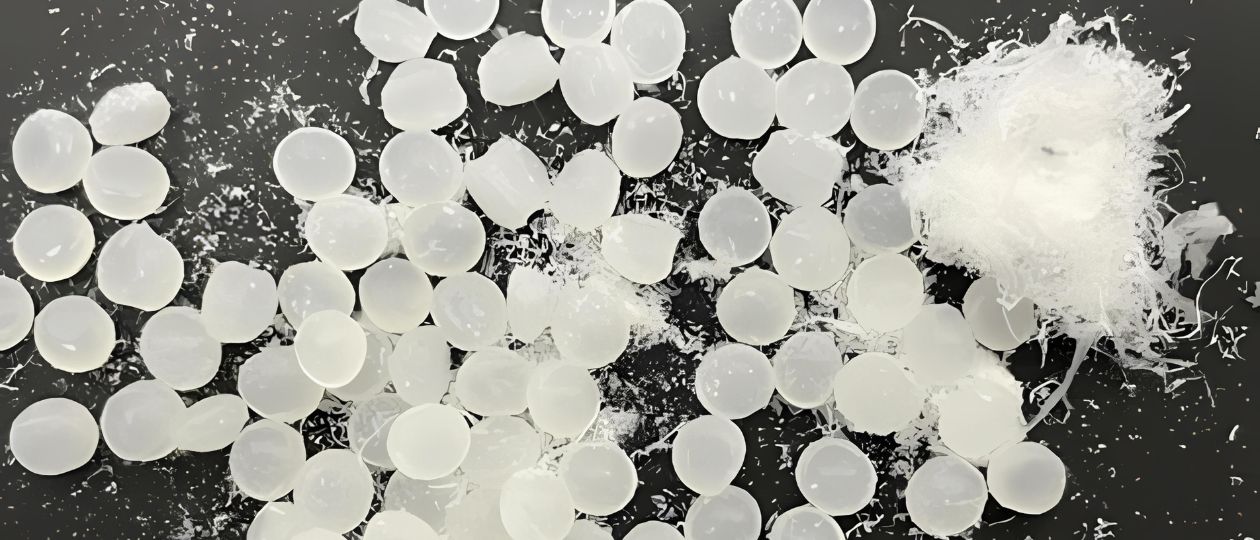
3. Dimensional Inaccuracy
Dust Clumping:
- Agglomerated dust can create localized density variations, causing warping or shrinkage inconsistencies.
- Critical for precision components like gears or connectors, where even 0.1mm deviations cause assembly failures.
Streamer-Induced Flow Restrictions:
- Strand-like streamers obstruct narrow channels in molds, leading to incomplete parts (“short shots”).
4. Aesthetic and Functional Failures
Discoloration:
- Dust absorbs moisture or reacts with additives, causing yellowing or blotchy pigmentation in transparent/colored plastics.
Electrical and Optical Issues:
- Dust in conductive plastics (e.g., housings for electronics) can create short circuits or interfere with signal transmission.
- Streamers in optical-grade plastics (e.g., lenses, light guides) scatter light, reducing clarity and performance.
5. Increased Scrap Rates and Rework Costs
- Contaminated pellets force manufacturers to reject defective batches, inflating material waste.
- Post-production polishing or re-machining to fix surface flaws adds labor and time costs.
Mitigating the Impact
- Advanced Filtration Systems: Use nano-level filters to trap sub-micron dust particles.
- Melt-Filtration Technology: Install automatic screen changers to capture streamers during extrusion.
- Quality Testing: Implement spectroscopy or microscopy to detect contaminants in raw pellets pre-production.
2. Extended Equipment Lifespan
Dust and debris accelerate wear and tear on machinery.
- Clogged Nozzles/Filters: Dust accumulation in extruders or injection molds leads to downtime for cleaning.
- Corrosion: Abrasive particles damage barrels, screws, and other components, increasing maintenance costs.
- Streamer Tangles: Strand-like streamers can jam hoppers or feed systems, halting production.
By using clean pellets, manufacturers reduce equipment stress and lower long-term operational costs.
3. Operational Efficiency & Cost Savings
Contaminant-free pellets streamline workflows:
- Reduced Downtime: Fewer machine stoppages for cleaning or repairs.
- Consistent Throughput: Smooth material flow prevents uneven melting or feeding issues.
- Energy Efficiency: Clean pellets melt uniformly, cutting energy waste from overheating.
A 2021 study found that dust-related delays cost manufacturers up to 15% in lost productivity annually.
4. Compliance with Industry Standards
Regulatory bodies (e.g., FDA, EU plastics directives) mandate strict purity levels for plastics used in food packaging, medical devices, and automotive parts.
- Safety Risks: Dust-contaminated plastics can leach harmful chemicals or fail safety tests.
- Certification Loss: Non-compliance may result in fines, recalls, or revoked licenses.
Clean pellets ensure adherence to global standards, protecting both consumers and corporate reputation.
5. Sustainability & Waste Reduction
Dust and streamers contribute to material waste:
- Recyclability: Contaminated plastic scraps are harder to recycle, increasing landfill burden.
- Resource Efficiency: Cleaner production lines generate less scrap, aligning with circular economy goals.
Companies prioritizing pellet cleanliness often achieve higher ESG (Environmental, Social, Governance) ratings.
6. Customer Satisfaction & Brand Reputation
Defective products damage trust:
- Fewer Returns: High-quality outputs reduce customer complaints.
- Competitive Edge: Brands known for consistency gain long-term partnerships.
A single recall due to contamination can cost millions and tarnish a company’s image irreparably.
Best Practices for Ensuring Pellet Cleanliness
1. Pre-Screening: Use vibrating sieves or air classifiers to remove larger particles before processing.
2. Wise use of pneumatic conveying: Use pneumatic conveying strategically in production facility to minimize dust and angel hair formation.
3. Use Plastic Pellet Cleaning Technology: Use PelletPurge® technology to clean particulate products before they enter storage, manufacturing, or packaging stages.
4. Proper Storage: Keep pellets in sealed, humidity-controlled containers to prevent contamination.
In an industry where precision and reliability are paramount, clean pellets are not just an option—they’re a necessity. From cutting costs to safeguarding reputations, investing in dust- and streamer-free materials pays dividends at every stage of production. Plastic manufacturers must prioritize pellet cleanliness to thrive in a competitive, quality-driven market.