Common Powder Flow Problems
Posted on by Indpro
Common Powder Flow Problems and Effective Flow Control Solutions
Powders are present everywhere in different industries, such as chemicals, pharmaceuticals, minerals, food processing and manufacturing. However, managing the flow of powders can be challenging due to their unique properties. We will explore some common powder flow problems encountered in industrial processes and discuss effective flow control solutions to mitigate these issues.
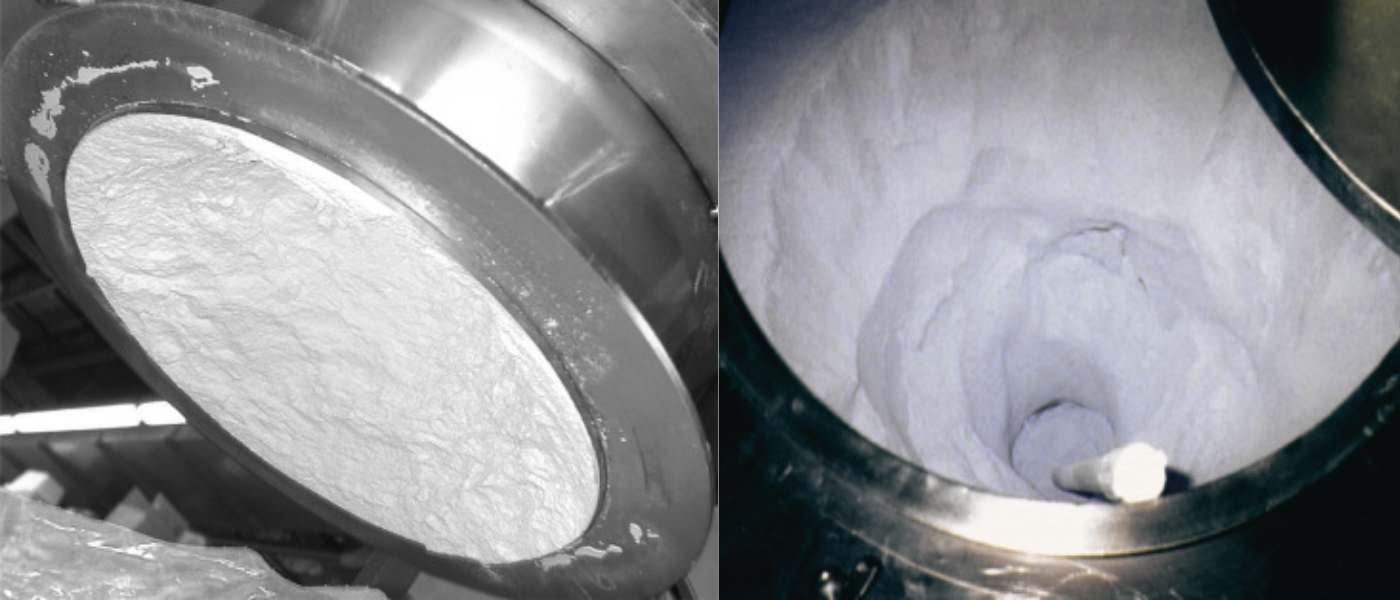
Common Powder Flow Problems:
1. Arching and Bridging:
- Arching occurs when a stable bridge forms over the outlet of a powder container, preventing the material from flowing freely.
- Bridging is similar but involves a wider area of material blockage.
- Common causes: cohesive powders, high moisture content, irregular container shapes, insufficient flow channel available.
2. Rat-holing:
- Rat-holing happens when a vertical channel forms in the powder material, causing uneven flow.
- It can lead to inconsistent dosing and inefficient processing.
- Factors: wide particle size distribution, improper hopper design, and insufficient vibration.
3. Segregation:
- Segregation refers to the separation of particles based on size or density during handling or movement, leading to uneven composition.
- It affects product quality and consistency.
- Contributors: differences in particle size, shape, and density, as well as vibration during transport.
4. Flow Rate Fluctuations:
- Uneven flow rates can impact production processes and result in inaccurate dosing.
- Inconsistent flow rates can stem from variations in powder properties or inadequate equipment design.
5. Flow Stagnation:
- Some powders tend to stick to the walls of containers, causing flow stagnation and reducing discharge rates.
- Fine particles and cohesive powders are prone to this issue. Moisture in powders also makes them stick to surfaces.
Effective Flow Control Solutions:
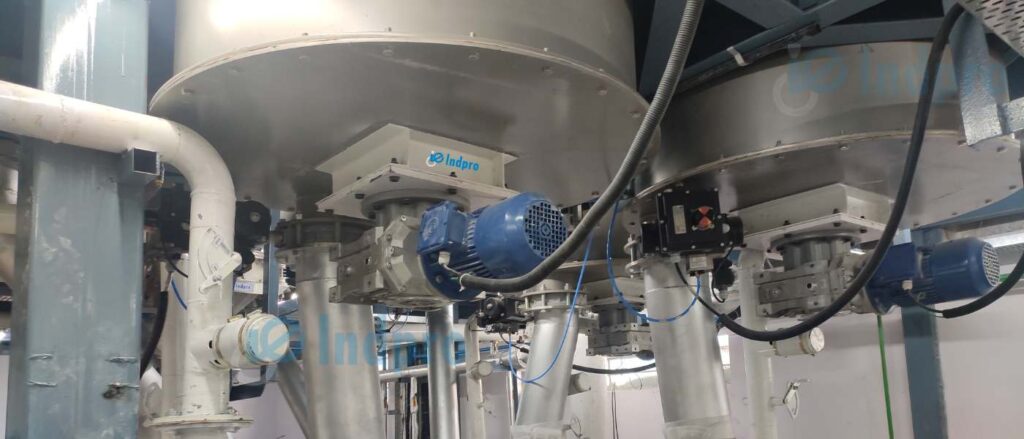
- Discharging powder materials from storage silos and hoppers in a controlled manner.
- It has a bottom panel with thin, radial vanes that revolve inside the hopper.
2. Hopper Design Optimization:
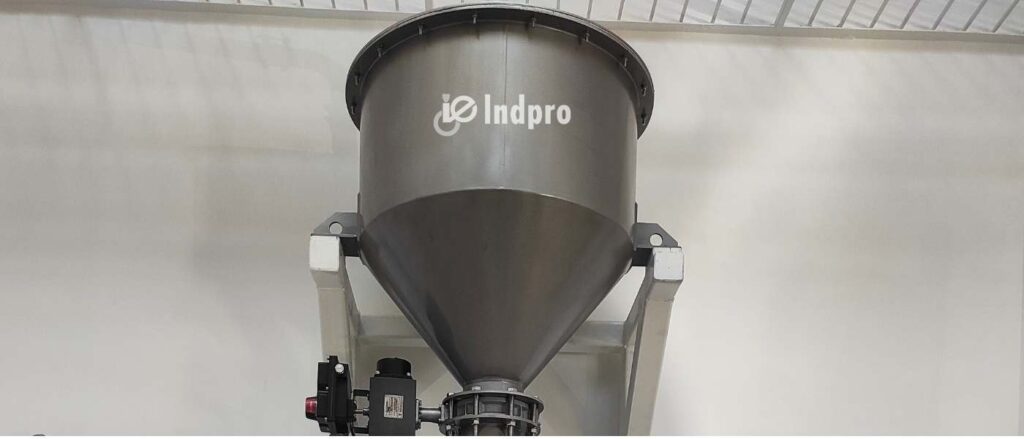
- Use hopper geometries that minimize dead zones and encourage mass flow.
- Conical hoppers with appropriate angles can prevent arching and encourage uniform discharge.
3. Vibration and Agitation:
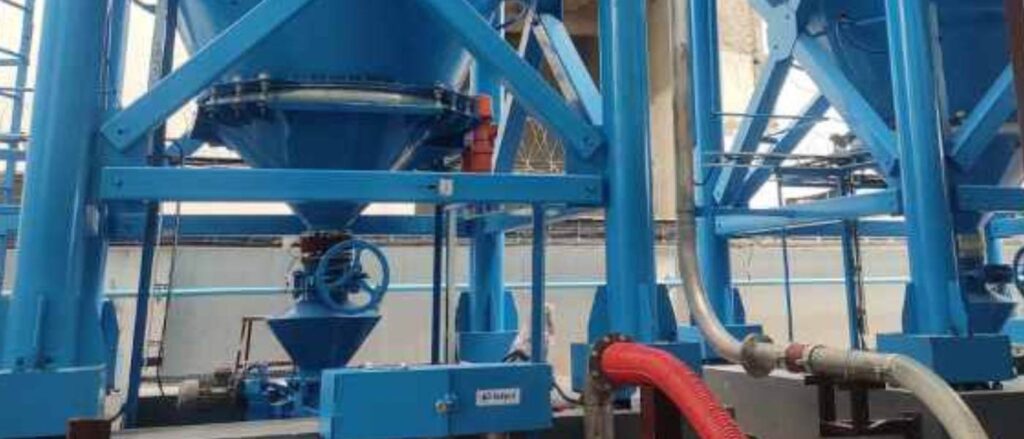
- Mechanical vibrations help in breaking arches, improving flow.
- Vibrating devices or agitators can be strategically placed to prevent rat-holing and maintain consistent flow.
4. Air Fluidization:
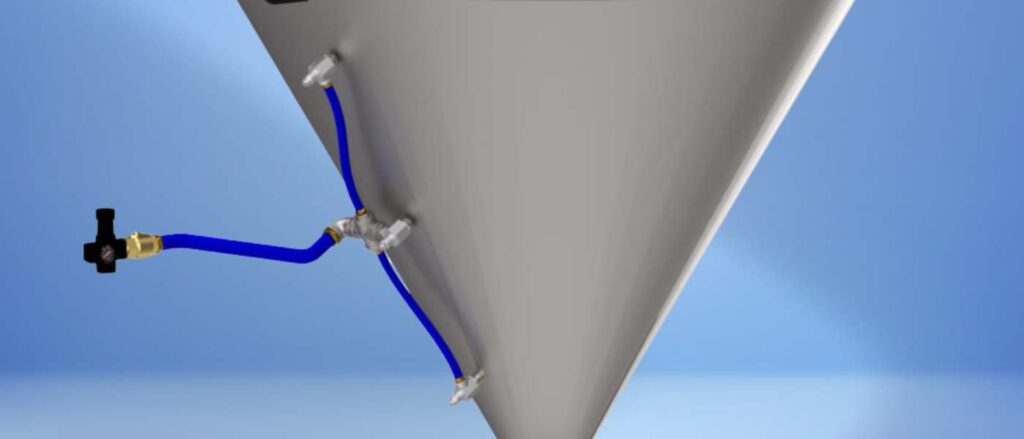
- Injecting air into the powder bed can reduce cohesive forces and enhance flowability.
- It is particularly effective for fine and cohesive powders.
5. Segregation Prevention:

- Minimize particle size and density variations through proper blending techniques.
- Maintain consistent flow velocities during transport to prevent particle separation.
6. Equipment Selection and Maintenance:

- Choose equipment that suits the powder’s properties and flow requirements.
- Regular maintenance of equipment prevents accumulation and blockages.
7. Testing and Analysis:

- Conduct flow tests to understand the powder’s behavior under different conditions.
- Use data to optimize flow control strategies.
Ensuring powder flow problems is crucial for maintaining efficiency and product quality across industries. By understanding the underlying causes of common issues and implementing effective flow control solutions, companies can enhance their production processes and reduce operational challenges associated with powder handling.