Different Prime Movers used in Pneumatic Conveying of Materials
Different Prime Movers used in
Pneumatic Conveying of Materials
Pneumatic conveying systems facilitate the movement of bulk materials like powder, pellets, granules grains, spices, etc. through enclosed pipelines using gas, typically air or nitrogen. Widely employed in various industries, these systems leverage gas pressure differential and flow to transport granular or powder materials. This article delves into the diverse prime movers used in pneumatic conveying systems, exploring their working principles.
What is Prime Mover?​​
Prime mover is a vital part of pneumatic conveying system. These prime movers serve as the driving force to propel gas within the pipelines in pneumatic conveying systems. The key types include compressors, blowers, and vacuum pumps.
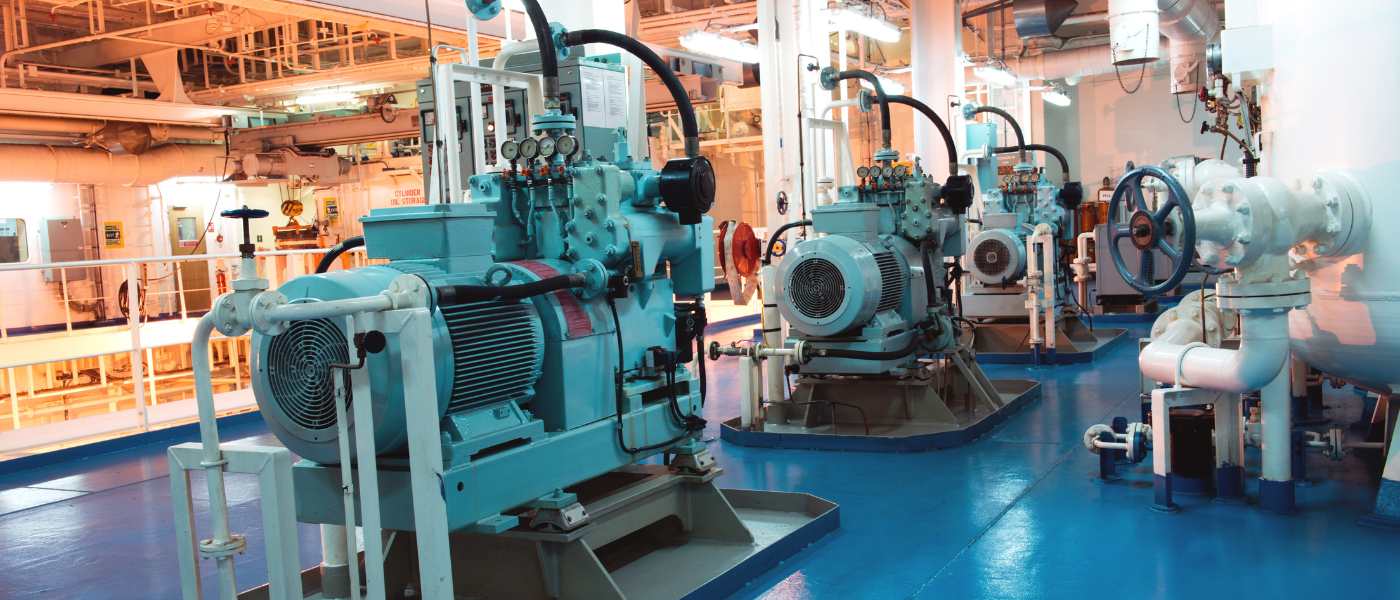
Types of Prime Mover -
1. Vacuum pump: Function, Working principle & Types​
Function of Vacuum Pump – A vacuum pump is a device designed to eliminate gas molecules or air particles from a sealed volume, creating a pressure difference and generating a partial vacuum.
Working Principle & Types of Vacuum Pumps
The fundamental principles of vacuum pumping can be broadly classified into two main categories: gas transfer and entrapment. Gas transfer itself can be subdivided into two distinct methods known as positive displacement and momentum transfer. Understanding the three types of flow: viscous, transitional, and molecular—provides a deeper insight into the concepts of vacuum pumps.
Viscous/continuous flow:
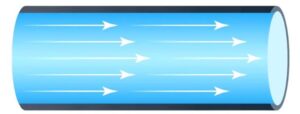
Viscous flow takes place at high pressures to medium vacuum levels. In this scenario, the gas is dense enough for gas molecules to collide with each other. The mean free path, which represents the average distance a gas molecule travels, is shorter than the dimensions of the chamber. As the vacuum level increases, gas molecules are more likely to collide with the chamber walls than with other gas molecules.
Transitional flow:
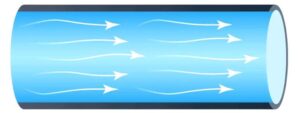
Transitional flow occurs when viscous flow begins to transition into molecular flow. This shift happens as the mean free path of gas molecules becomes comparable to or exceeds the dimensions of the chamber.
Molecular flow:
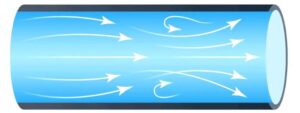
Molecular flow is defined by the random motion of gases, where the mean free path of gas molecules is notably greater than the dimensions of the chamber. In this scenario, collisions between gas molecules are infrequent, and their movement is primarily determined by the chamber’s geometry. Positive displacement pumps can mechanically pump fluids that are flowing under viscous conditions. However, when the gas cannot be evacuated by pressure difference, molecular flow is reached When fluids transition into molecular flow, positive displacement pumps become inadequate. In such situations, additional pumping systems like momentum transfer or entrapment pumps are employed to maintain the required vacuum levels. Â In most high vacuum systems, two pumps are typically employed together. Positive displacement pumps alone prove insufficient for achieving higher vacuum levels. Momentum transfer pumps run the risk of stalling when the system operates under viscous flow conditions. Entrapment pumps may require frequent regeneration or emptying, particularly when dealing with high gas volumes, especially in situations involving viscous flow.
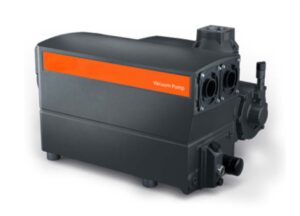
i. Positive Displacement Vacuum Pumps:
Positive displacement vacuum pumps function by alternately expanding and contracting a sealed chamber, with the flow of fluid regulated by one-way valves. The process begins with the expansion of a sealed chamber, creating a vacuum that draws fluid through an intake valve. As the chamber reaches maximum expansion, the intake valve closes, and the exhaust valve opens. As the chamber compresses or contracts, the fluid is expelled. This cycle repeats multiple times per second, generating a pulsating flow. There are two main types of positive displacement pumps – Reciprocating (Piston Pump, Plunger Pump, Diaphragm Pump) & Rotary (Vane Pump, Liquid Ring Pump, Rotary Piston Pump, Screw Pump, Gear Pump, Lobe Pump)
ii. Momentum Transfer Vacuum Pumps:
Momentum transfer pumps operate by inducing the movement of gas or liquid molecules through the transfer of kinetic energy. This occurs at the molecular flow level, in contrast to the viscous or continuous flow observed in positive displacement pumps. Its types include Turbomolecular Pump & Diffusion Pump.
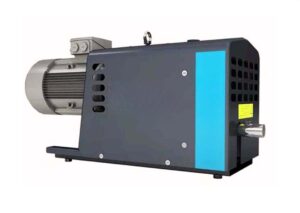
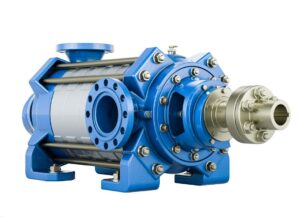
iii. Entrapment Vacuum Pumps:
Entrapment vacuum pumps utilize various physical and chemical phenomena to capture gas molecules. These pumps operate in high vacuum regimes without causing oil contamination. Its types include Cryogenic pump, Sorption Pump, Sputter Ion Pump, Centrifugal Pumps.
2. Blower: Function, Working principle & Types
- Function of Blower : Function of blower is to move air and gas at low to high pressure to perform a specific function. Blowers play a versatile role in numerous industries, serving various applications such as cooling, conveying, ventilating, exhausting, and more.
- Working Principle of Blower: An air blower utilizes a rotating impeller or rotor to generate a vacuum, drawing air into the blower. As the air enters the center of the impeller, it is separated by the rotating blades. The centrifugal force increases both the speed and volume of the air stream within the housing
Types of Blowers -
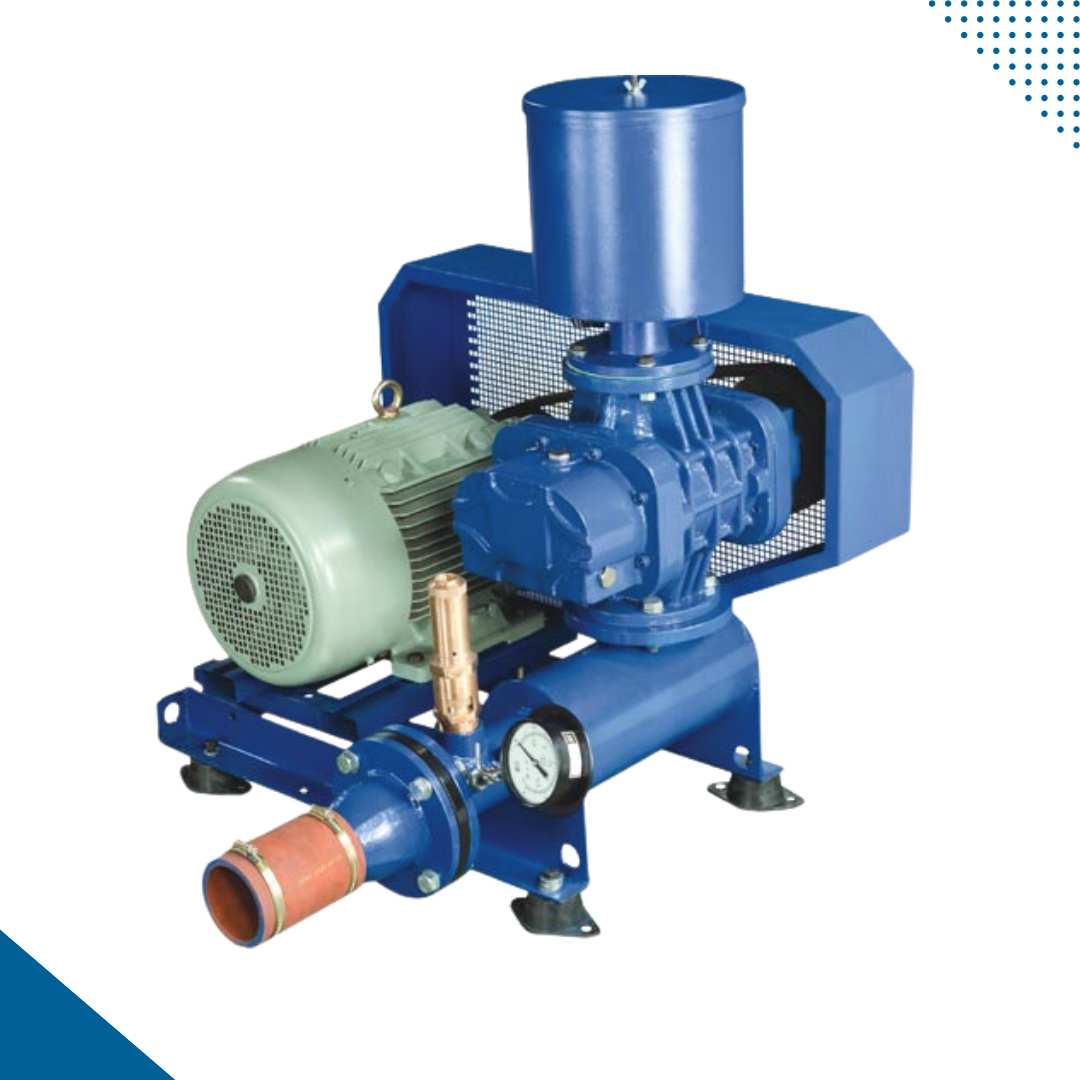
i. Positive Displacement Blowers:
A positive displacement blower operates to maintain a consistent flow and speed regardless of changes in pressure. This characteristic makes it well-suited for moving neutral and air gases. The blower effectively removes gas through the decreasing section, trapping and releasing air in a cyclical manner. There are two distinct types available – the Rotary Lobe Blower and the Helical Screw Blower.
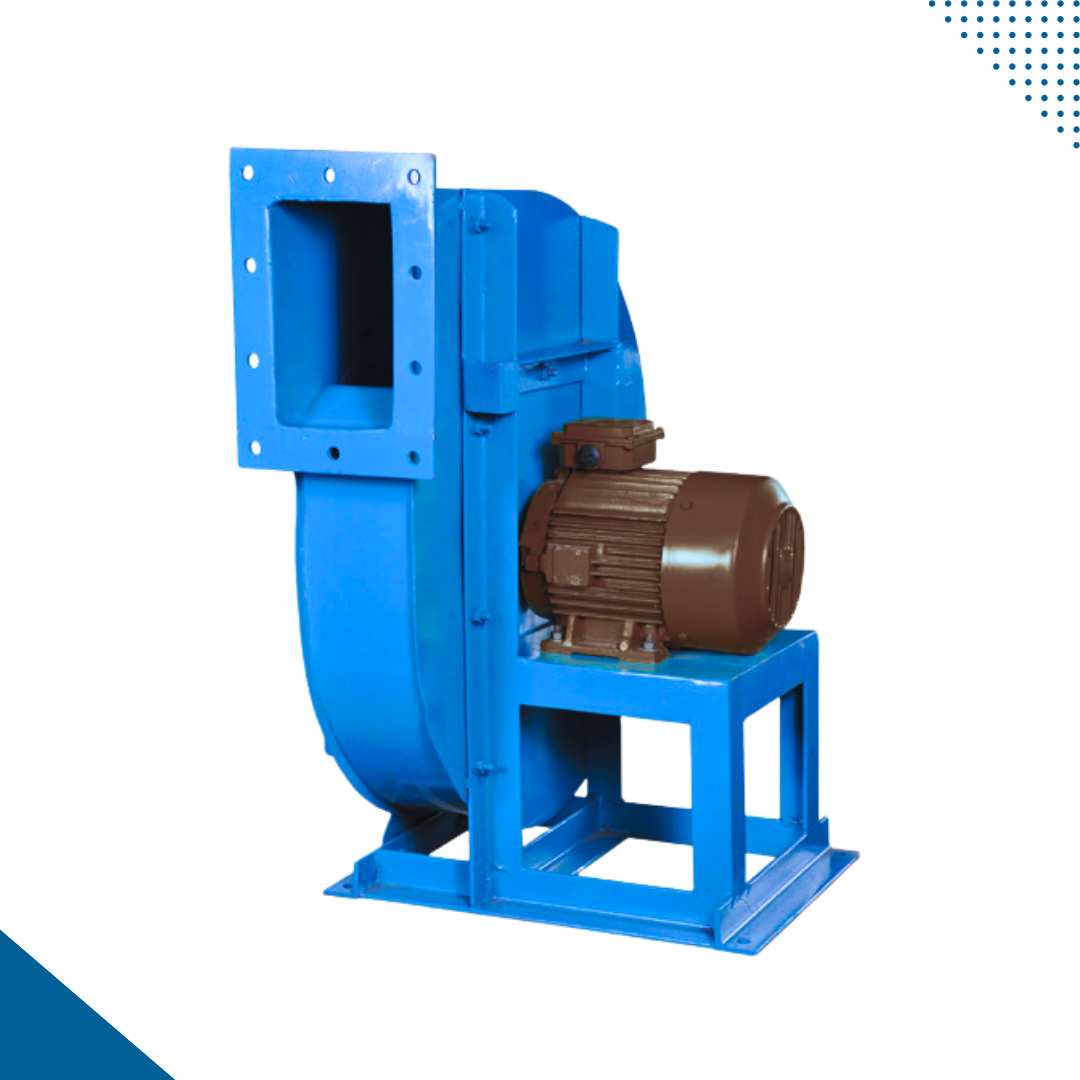
ii. Centrifugal Blowers:
A centrifugal blower is effective in controlling air pollution and facilitating gas transportation. This type of blower is commonly employed for ventilation purposes, operating by altering the direction of airflow with a 90-degree turn. Continuous gas transfer is achieved as the gas passes through the centrifugal blower, increasing kinetic energy. Equipped with rotating impellers, these blowers are suitable for applications requiring variable flow with high pressure.
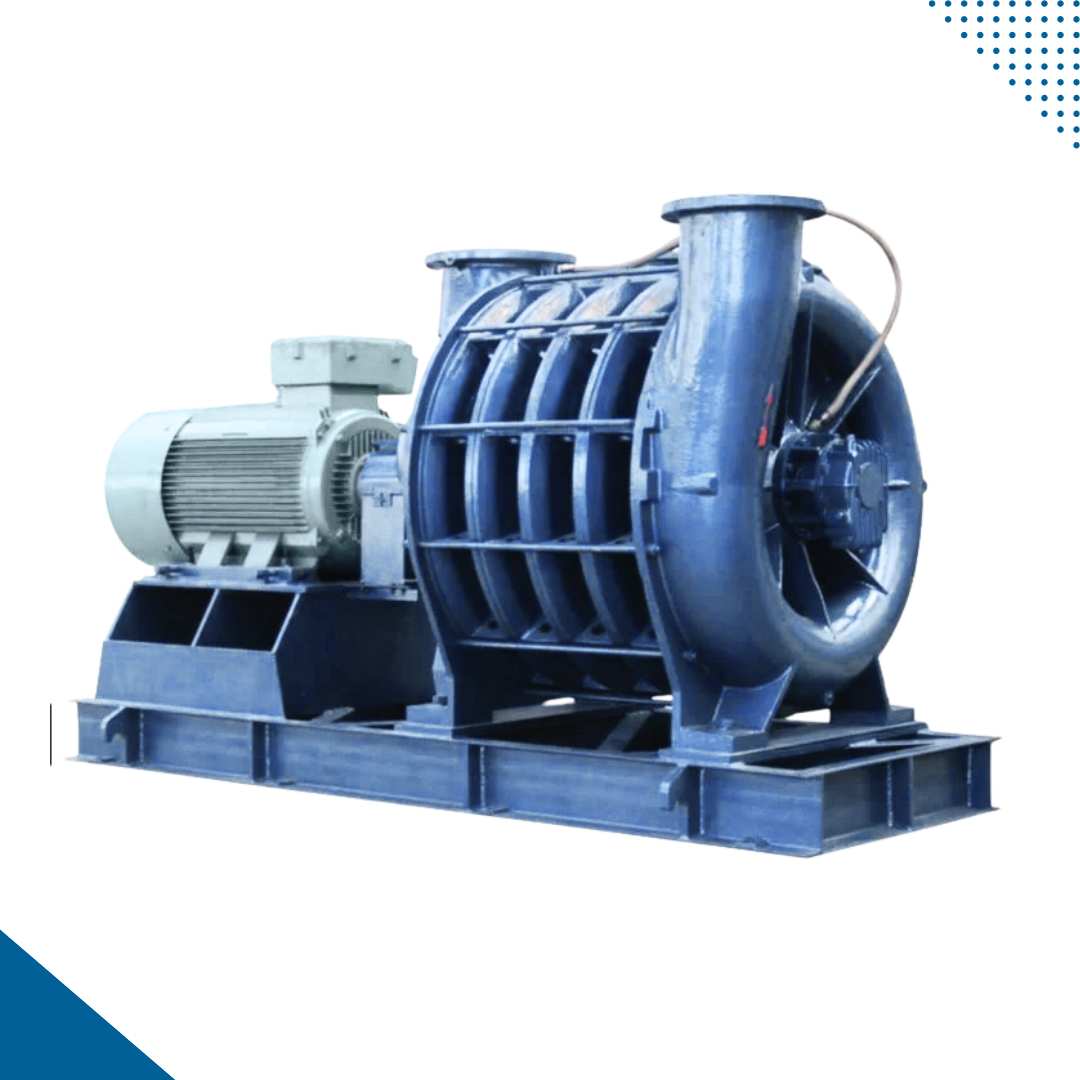
iii. Multistage Centrifugal Blowers:
Multistage centrifugal blowers are a specific type within the centrifugal blower category. These blowers utilize multiple stages to rotate the machine and increase air pressure. Equipped with an electric motor that provides high-pressure tolerance, they are suitable for applications with high flow rates. Multistage centrifugal blowers find utility in various sectors, such as the wastewater treatment industry, powering artificial lungs, and boosting landfill gas.
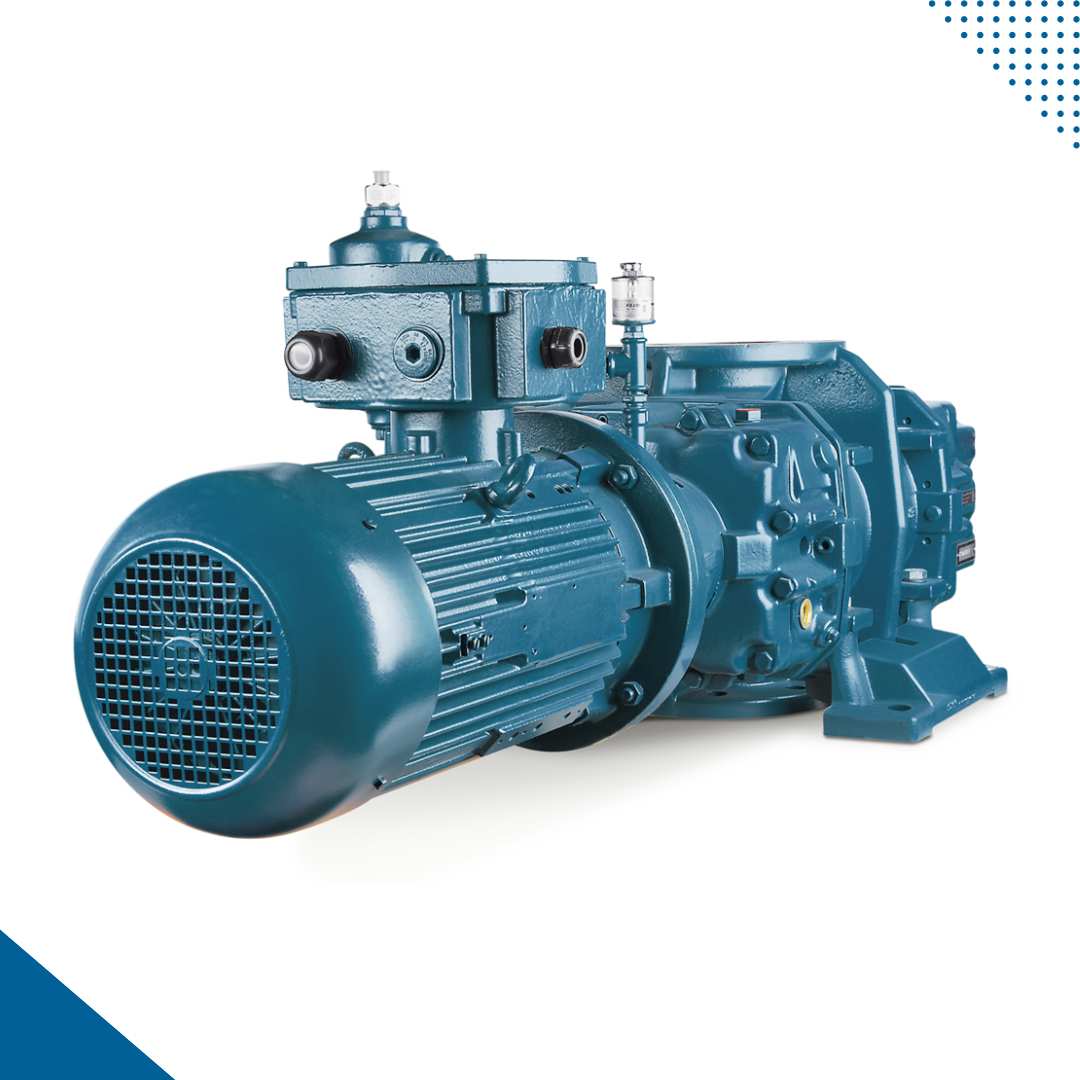
iv. High-Speed Blowers:
High-speed blowers are designed to provide both high pressure and high flow, making them versatile for various applications. These blowers typically feature impellers on each side, directly coupled to a motor. The ability to connect them to a permanent magnet motor with a variable frequency drive allows for efficient control and adjustment based on specific operational needs.
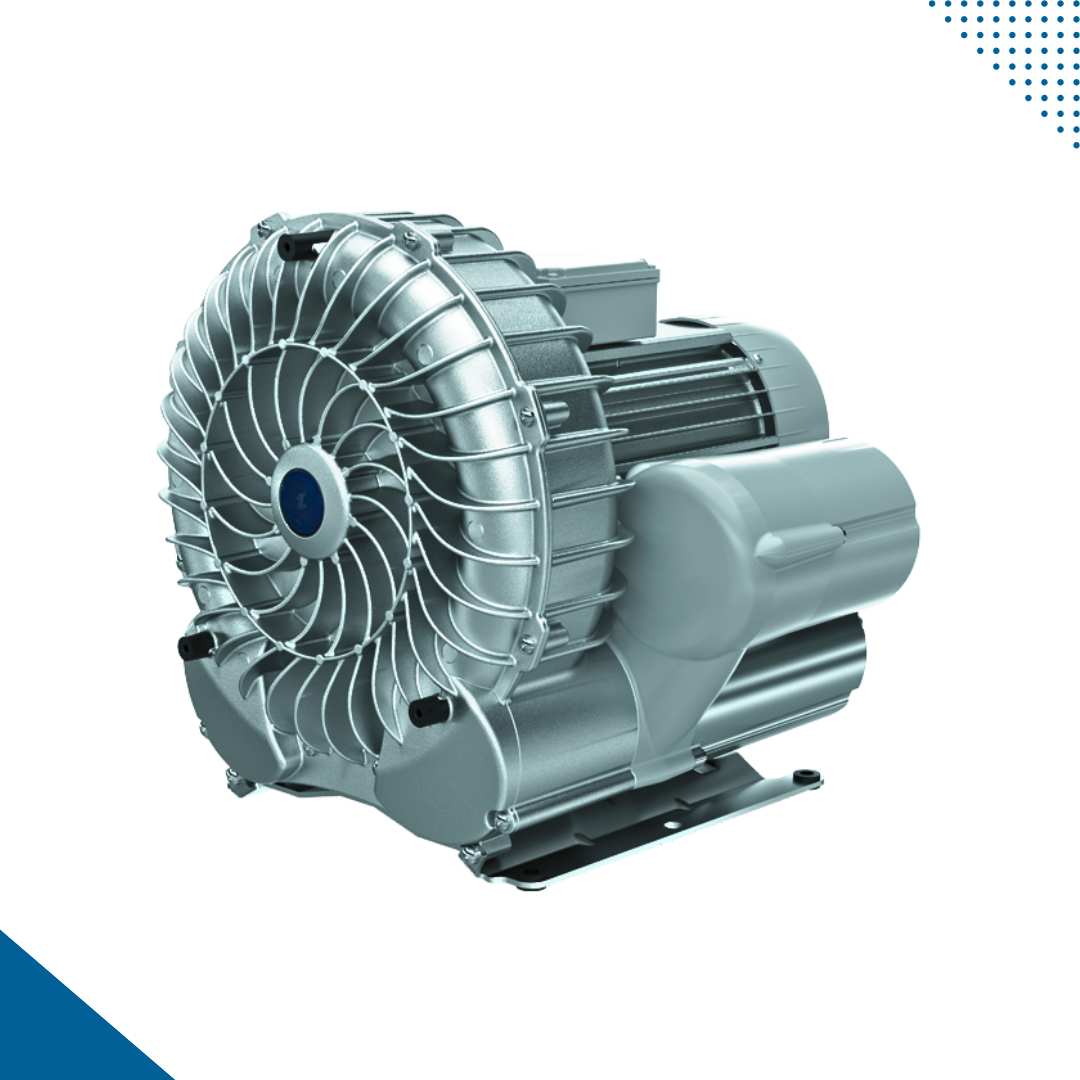
v. Regenerative Blowers:
A regenerative blower is characterized by oil-free components, making maintenance relatively easy. Ideal for applications requiring low pressure, these blowers operate by displacing air molecules and creating pressure through non-positive displacement, forcing the air to move.
3. Compressor: Function, Working principle & Types
- Function of Compressor: A compressor is a device designed to compress air or other gases, elevating their pressure beyond atmospheric levels. It takes in air from the atmosphere and increases its pressure through compression.
- Working principle & types of compressors: To explain the working principle of air compressors, it’s crucial to differentiate between various types of compressors: reciprocating (piston) and rotary (screw) compressors.
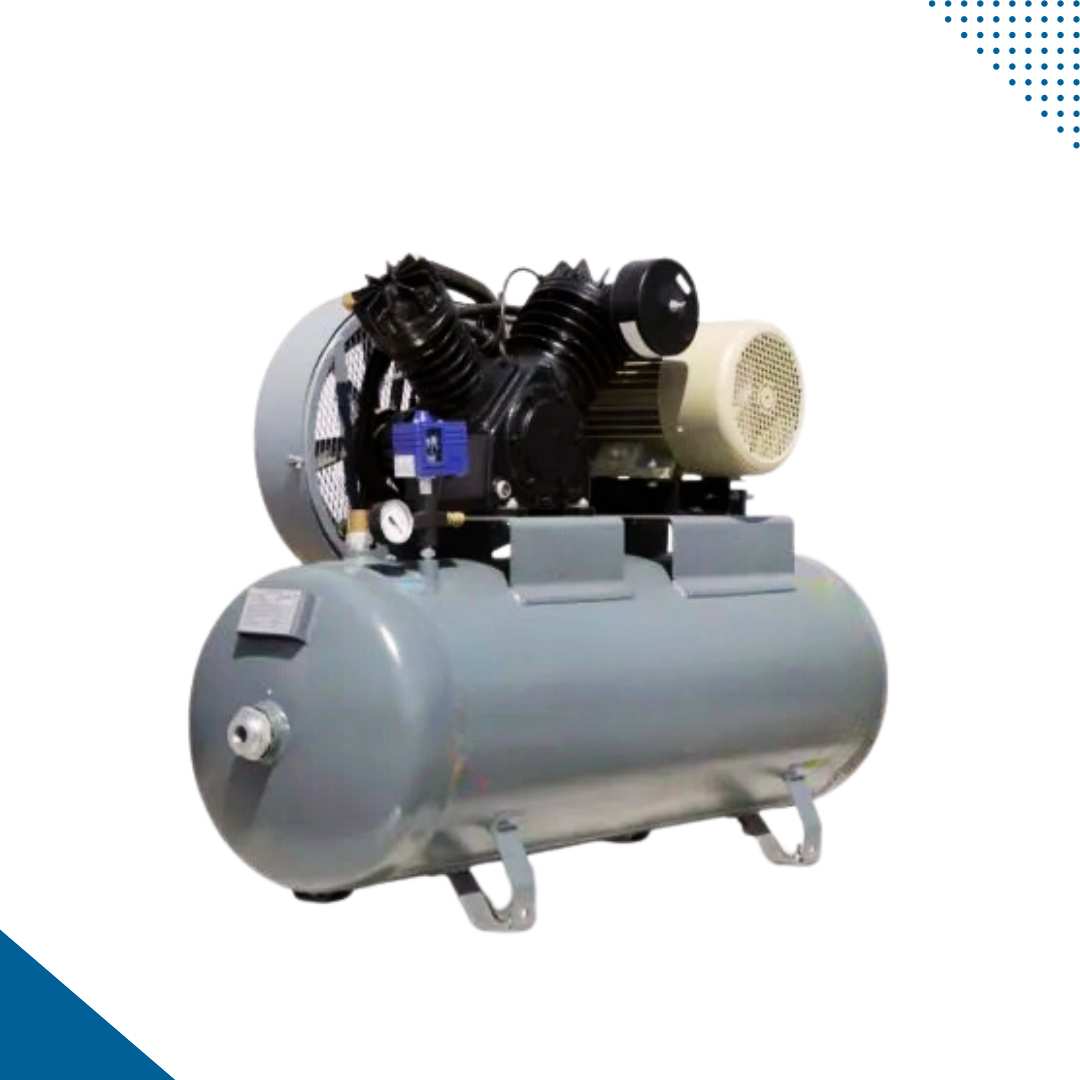
i. Reciprocating Compressor:
In a reciprocating compressor, air compression occurs through cylinders, pistons, and cranks. These components, driven by an electric or combustion engine, draw air into the cylinder and compress it using pistons. The compression process may consist of one or multiple stages until the desired operational pressure is reached. The compressed air then passes through a cooler into the air tank. These are used by many industries which includes Chemical, Petrochemical, Oil & Gas, Refrigeration, etc. Reciprocating compressors come in various types, including Single Acting, Double Acting, Single Stage, and Double Stage.
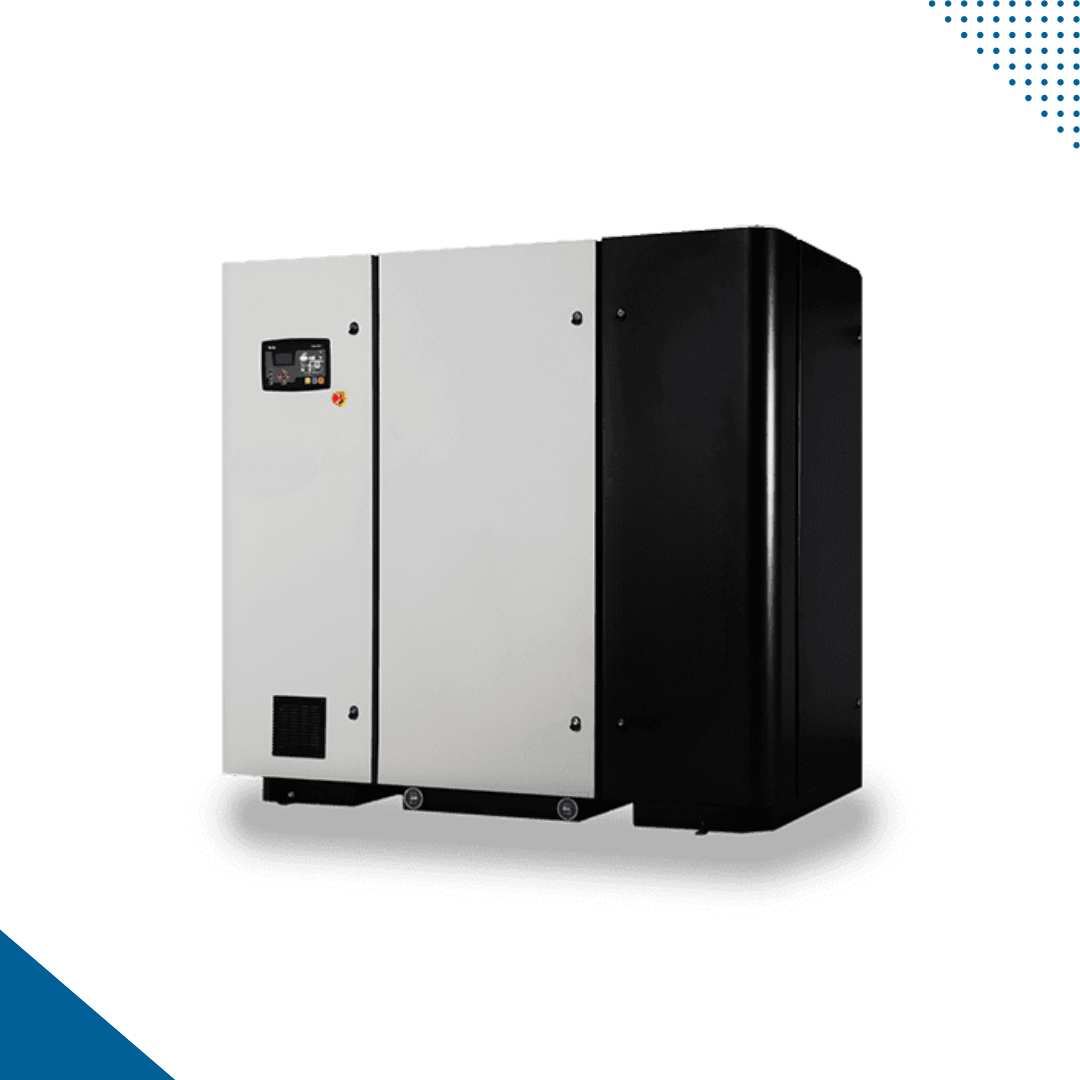
ii. Rotary Compressor:
Rotary compressors operate differently from reciprocating compressors. Instead of using pistons and cylinders for compression, rotary compressors employ rotating screws to initiate compression. Air is forced between two rotating screw elements, resulting in compressed air. As the compression generates heat, a cooling liquid, often oil, is injected into the compression chamber. This cooling liquid circulates between the cooling chamber, liquid tanks, and coolers to maintain the operating temperature around 80°CThese are utilized in various industries, including the food sector. Packaging sector, Automotive sector, etc. The types rotary compressors include Rotary Screw compressor which is most widely used, Scroll Type compressors, Vane Type compressors & Lobe Type compressors.
Selecting the Right Prime Mover for Pneumatic Conveying System
Choosing the appropriate prime mover for your specific system is of greatest importance in optimizing operational efficiency and lifespan of equipment. Below are some guidelines for selection of right prime mover for pneumatic conveying system:
Fan
It is used when working with dilute phase pneumatic conveying systems (both pressure as well as vacuum based) with low solids-to-air ratio
Lobe Blower
It is used when working with dilute phase pneumatic conveying system (both pressure as well as vacuum based) with high solids to air ratio
Vacuum Pump
It is used when working with dense phase vacuum type pneumatic conveying system
Compressor
It is used when working with dense phase pressure type pneumatic conveying system