High-Quality Fabrication – Key for the success of Pneumatic Conveying Systems
High-Quality Fabrication - Key for the success of
Pneumatic Conveying Systems
Fabrication manufacturing is an essential part of creating components crucial to the operation of pneumatic conveying systems (PCS). From Silo, hoppers to ductwork, these fabricated components are vital for the efficient transport of bulk materials across industries. Let’s explore the fabrication process and its significance in the world of PCS.
1. What is Fabrication? And Why is Fabrication Quality Important in Pneumatic Conveying Systems?
Fabrication involves the assembly of sheet metal parts to create products, structures, or components that meet specific design criteria. Key steps in the fabrication process include cutting, shaping, joining, and assembling sheet metals to achieve the desired form and function of the final product.
Pneumatic conveying systems are complex and require precise engineering and fabrication to function properly. Any flaws or imperfections in the fabrication process can lead to issues such as material buildup, blockages, and leaks, which can result in costly downtime and maintenance.
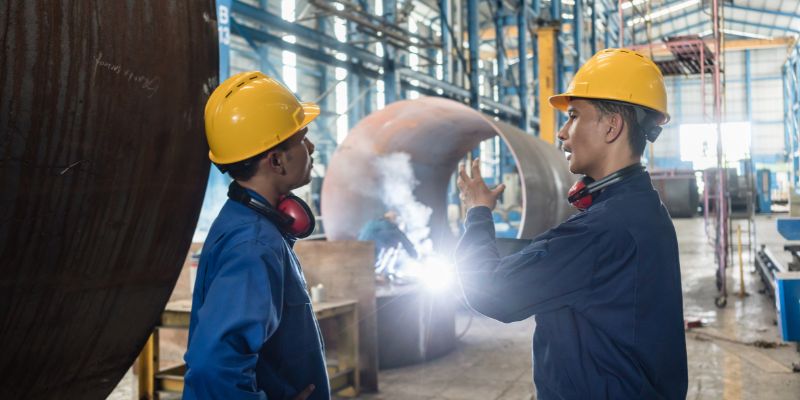
High-quality fabrication is essential for the success of conveying systems for the following reasons:
Efficient Material Flow:
The primary purpose of a pneumatic conveying system is to transport materials from one location to another. Any obstructions or irregularities in the hoppers and other storage devices can disrupt the flow of materials, leading to inefficiencies and potential system failures.
Proper fabrication techniques ensure that the surfaces in powder contact are smooth and free of any obstructions, allowing for efficient material flow and preventing costly downtime.
Durability and Longevity:
Pneumatic conveying systems are often used in industrial settings where they are subjected to harsh conditions and heavy use. This makes durability and longevity crucial factors in the success of these systems.
High-quality fabrication techniques, such as using corrosion-resistant materials and proper welding methods, can ensure that the system can withstand the demands of its environment and have a longer lifespan.
Safety:
Safety is a top priority in any industrial setting, and pneumatic conveying systems are no exception. Poor fabrication can lead to leaks, blockages, and other issues that can compromise the safety of workers and the surrounding environment, especially when handling hazardous powders.
By using high-quality fabrication techniques, the risk of accidents and injuries can be greatly reduced, making the workplace safer for everyone. Following the correct design and manufacturing practices for explosion protection is of paramount importance.
Key Fabrication Techniques for Pneumatic Conveying System Components
Achieving high-quality fabrication in pneumatic conveying requires a combination of advanced techniques and skilled craftsmanship. Here are some of the key techniques used in the fabrication of these systems:
Metal Shaping:
Metal shaping is a crucial step in the fabrication process of pneumatic conveying system components. It involves using various tools and techniques to bend, cut, and shape metal sheets into the desired form.
The most common metal shaping techniques include:
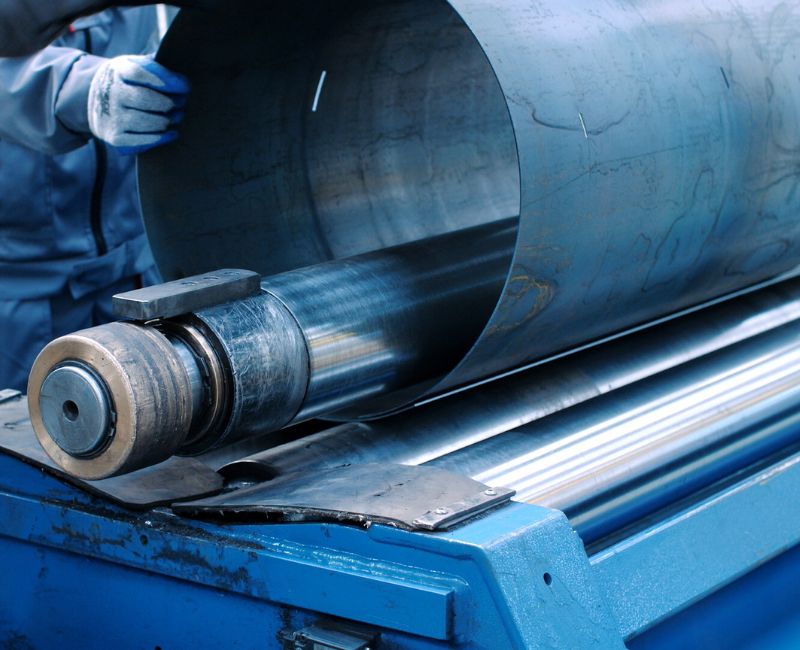
Rolling
This technique involves passing a metal sheet through a set of rollers to bend it into a cylindrical shape, which is commonly used for the fabrication of pipelines.
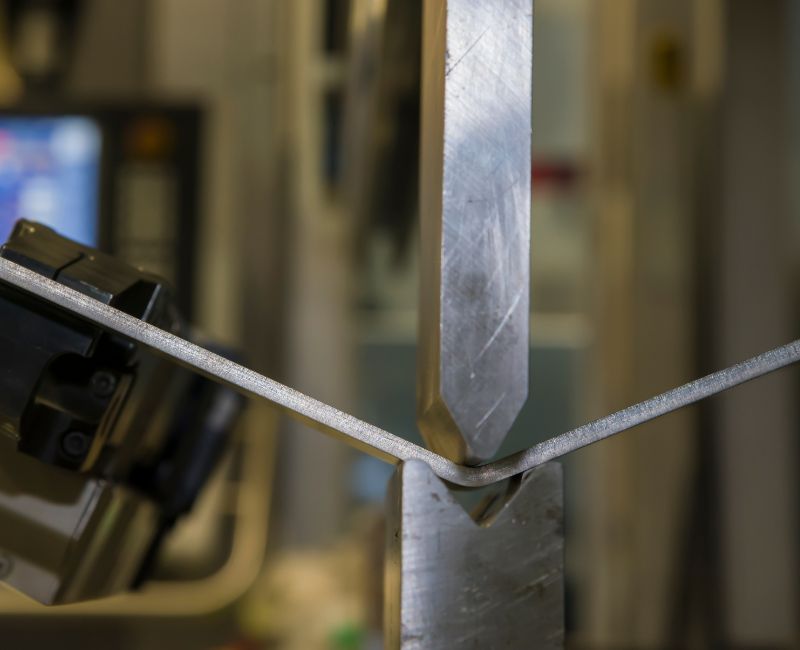
Bending
Bending is the process of using a press brake or other tools to create bends and angles in metal sheets.
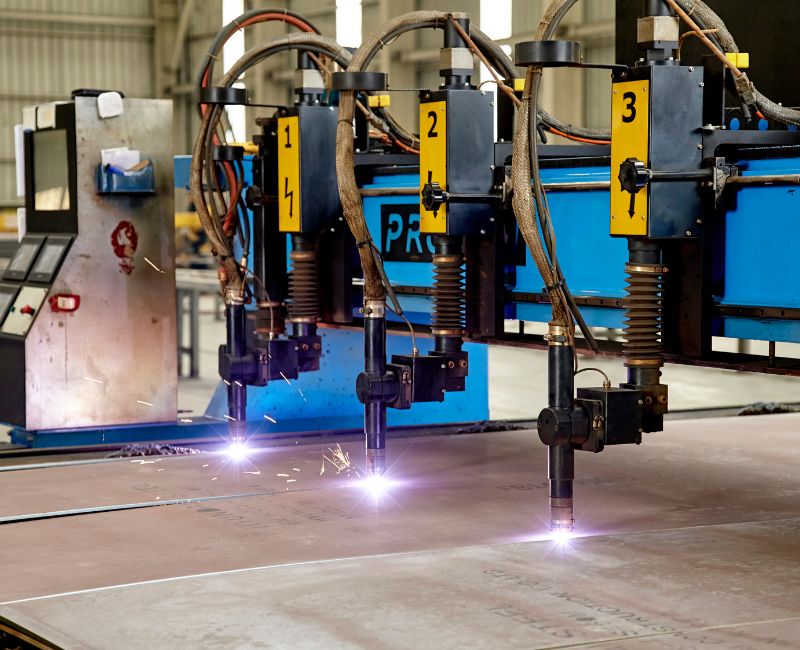
Cutting
Cutting is used to trim metal sheets to the desired size and shape using tools such as shears, plasma cutters, or laser cutters.
Proper metal shaping is essential for creating a smooth and seamless component, which is crucial for efficient material flow in pneumatic conveying systems.
Welding:
Welding joins individual metal components together to form the final structure. It is a critical step in the fabrication of pneumatic conveying systems, as it is used to create airtight seals and ensure the structural integrity of the system.
There are several welding techniques used in the fabrication including:
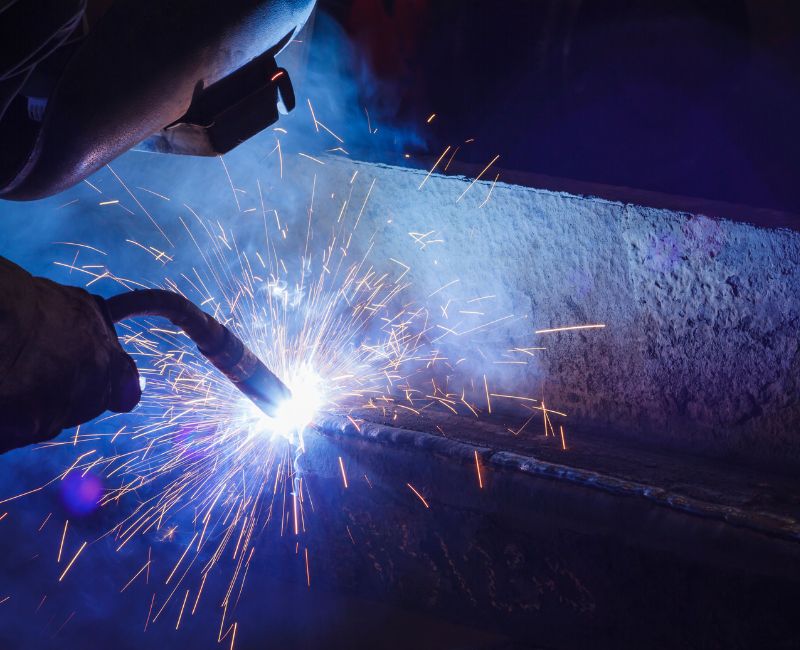
MIG Welding
MIG (Metal Inert Gas) welding is a popular technique that uses a wire electrode to create a strong and durable bond between metal pieces.
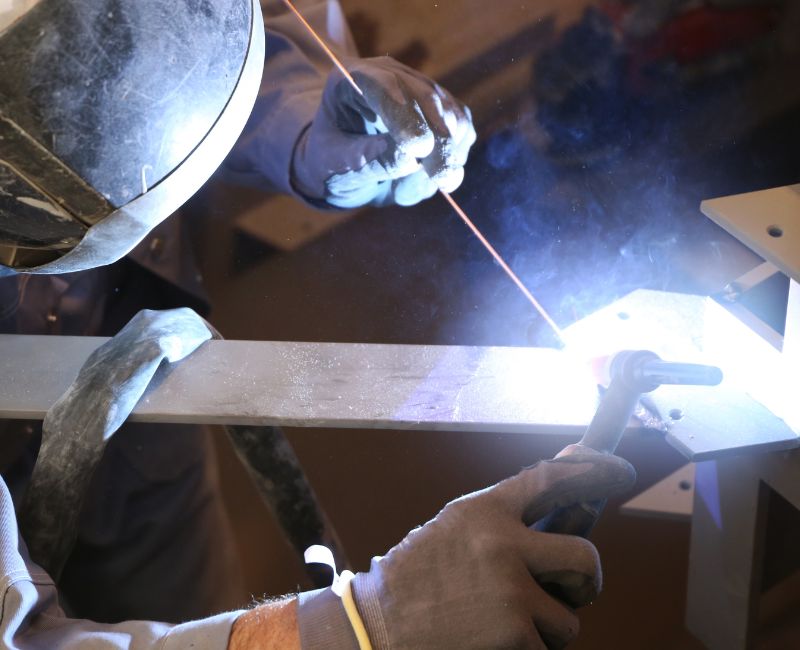
TIG Welding
TIG (Tungsten Inert Gas) welding is a more precise technique that uses a tungsten electrode to create a high-quality weld.
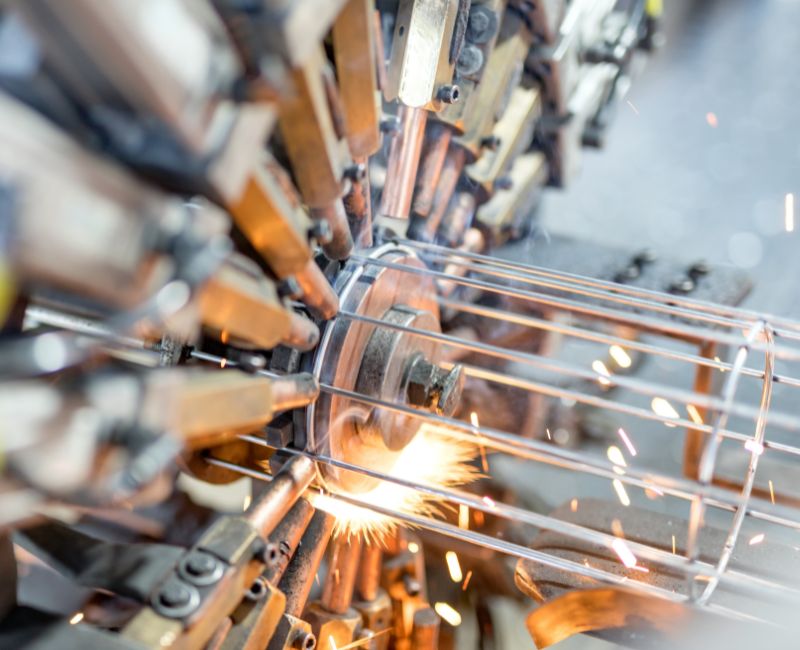
Resistance Welding
Resistance welding uses electrical resistance to join metal pieces together, making it a fast and efficient method for high-volume production.
Proper welding techniques are crucial for creating airtight seals and ensuring the structural integrity of the system, which is essential for the safe and efficient operation of conveying systems.
Finishing:
Finishing is the final step in the fabrication process of pneumatic conveying systems. It involves applying a protective coating or finish to the metal surfaces to improve their durability and resistance to corrosion.
Some of the most common finishing techniques used in the fabrication include:
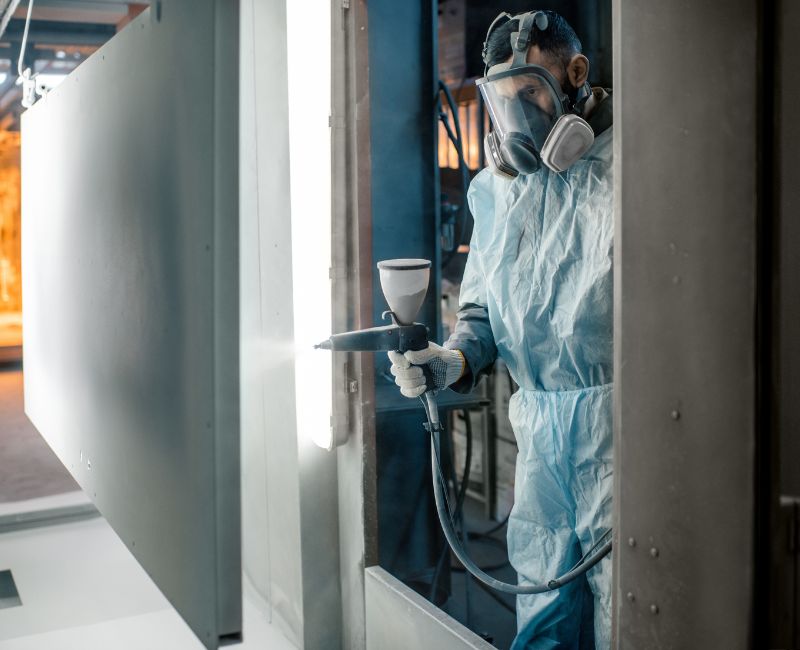
Powder Coating
Powder coating involves applying a dry powder to the metal surface and then curing it with heat to create a durable and attractive finish.
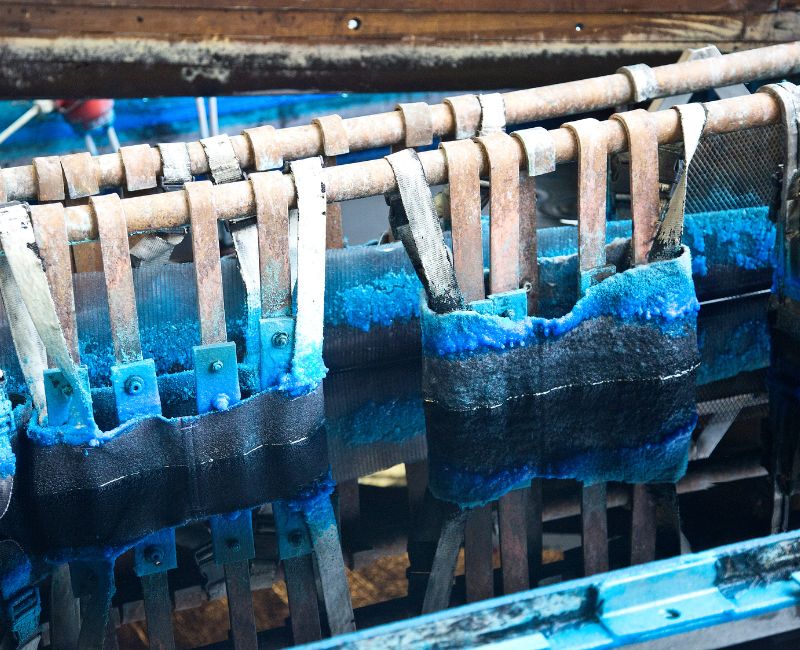
Galvanizing
Galvanizing is the process of coating metal surfaces with a layer of zinc to protect them from corrosion.
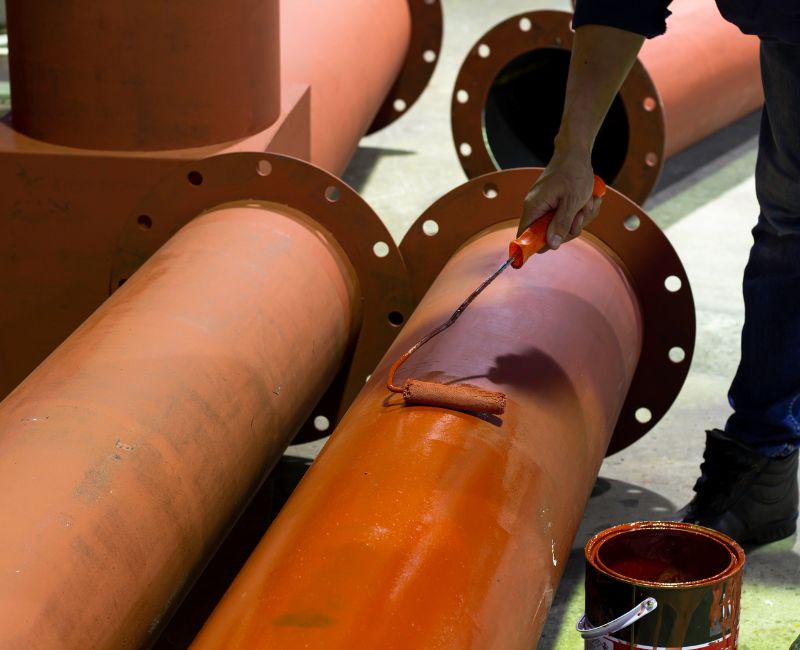
Painting
Painting is a cost-effective finishing technique that involves applying a layer of paint to the metal surface to improve its appearance and protect it from corrosion.

Polishing
The surface is grinded to reduce the roughness of the surface, hence improving the look, finish, and smoothness.
Proper finishing techniques are crucial for ensuring the longevity and durability of pneumatic conveying systems, especially in harsh industrial environments.
Real-World Examples of High-Quality Fabrication in Pneumatic Conveying Systems
One example of high-quality fabrication in pneumatic conveying systems is the use of stainless steel for the construction of components. Stainless steel is a durable and corrosion-resistant material that is commonly used in the fabrication for the food, chemical and pharmaceutical industries.
Another example is the use of advanced welding techniques, such as TIG welding, to create airtight seals in the components of conveying systems. This ensures that there are no leaks or blockages that can disrupt the flow of materials and compromise the safety of the system.
Who is Responsible for Fabrication?
The responsibility for fabrication falls on a team of skilled professionals, including engineers, fabricators, and welders. These individuals work together to design, engineer, and fabricate the system to meet the specific needs of the client.
Which components of Pneumatic conveying system are fabricated?
In a pneumatic conveying system, various components are fabricated to ensure efficient operation. Some of the key components that are typically fabricated include:
1. Pipelines:
The pipelines play a crucial role in transporting materials from one point to another in the system. Proper fabrication techniques are essential to create smooth and seamless pipelines to prevent material buildup and ensure efficient material flow.
2. Ductwork:
Ductwork is used to direct the airflow and materials within the system. Fabrication of ductwork involves shaping and welding to create the necessary pathways for material or dust transportation.
4. Valves and Dampers:
Valves and dampers control the flow of materials within the system. Fabrication of these components involves precision machining and welding to ensure proper functioning and minimal air leakage.
5. Centrifugal Blowers:
These are crucial for generating the air flow and pressure needed to transport materials. Fabrication techniques are used to assemble and integrate these components into the system effectively.
6. Silo and Hoppers:
Fabrication of silos involves structural integrity considerations to withstand the weight of stored materials and environmental factors. Hoppers hold the materials before they are conveyed, while feeders regulate the material flow into the system. Fabrication of hoppers and feeders involves structural integrity and durability considerations.
7. Support Structures:
Support structures hold the components of the system in place. Fabrication techniques are used to ensure that these structures are stable and able to withstand the operational stresses of the system.
8. Screw feeders:
These are mainly used in the system for transportation of powders mechanically or as a feeder in the conveying line. Fabrication quality is essential in maintaining the clearance and effectiveness of the unit.
9. Material receipt components:
Units such as bag dump stations, jumbo bag unloading systems and drum tilting stations, are used in conjunction with pneumatic conveying systems for powder unloading & transfer. The complex design and assembly of these units require good fabrication techniques.
10. Special devices:
There are many other components used as a part of the system, such as lump breaker, powder bridge breaker, bin activator, mixers, and many other. Fabrication techniques play a bigger role in ensuring quality of these products for use in the system.
High-quality fabrication is crucial for the success of pneumatic conveying systems. It ensures efficient material flow, durability and longevity, and the safety of workers and the surrounding environment. By using advanced techniques such as metal shaping, welding, and finishing, and working with a skilled fabrication team, you can ensure that your pneumatic conveying system is built to the highest standards and will provide reliable and efficient performance for years to come.