Spices Manufacturing Process
Spices Manufacturing Process
As food lovers, we Indians are devoted to spices. Spices play a significant role in our festivals, celebrations, and even daily lives. We may be divided by political boundaries, but the love for spices is a bond we share. Indian food is rich in spices unlike other markets, and this can be very well seen in the consumption pattern of spices. Textiles and perfumes are two of India’s largest exports in Spices. The market is exporting to places like Arabia, Sumeria, Mesopotamia, China, and Egypt.
Since the 1st century AD, spices have been discussed in Roman imperial literature. The Ramayana is one of the many sacred texts dedicated to spices. Spices were also delivered to distant places, such as Carthage, Alexandria, and Rome.
India is the world’s greatest producer of a wide range of species with the most varied aromas and flavours. Spices are grown and harvested in accordance with climatic conditions. The initial phase in this procedure is cleaning and drying, during which the spices are filtered and then dried. The spices are permitted in a crushing machine after they have been cleaned and dried.
With the growing demand, it is essential that the production must also keep up. Hence improving and enhancing spice production process requires plant automation. Cleaning, grinding, blending, sieving, material handling, and bulk storage, batch manufacturing, and packing are all automated procedures in spice processing, resulting in high quality and cleanliness of the finished product.
Indpro provides automated material handling systems for feeding silos, cleaning systems, mills, mixers for salt, starch, spices, and ingredients, and conveying systems for the finished spice combinations to packaging lines, as well as process leading visualization technologies. External and internal silos, loading stations for bags, jumbo bags, and weighing systems for ingredients and minor components are typical offerings from Indpro.
The materials used in the Spices industry –

Chilli Powder, Turmeric Powder, Chaat Masala, Mustard Powder, Coriander Powder, Turmeric Powder, Chaat Masala, Mustard Powder, Coriander Powder, Cumin, Fennel Seeds, Mixed Powder, Pepper, Poppy Seeds.
India's spice manufacturing industry faces several challenges:
1. Problems related to working labour
Experiencing the strong odour of spices for an extended periods of time can be harmful to health. As a result, it is difficult to find workers in the Indian spice industry.
2. Market credit
Spices have a high credit market risk with distributors, which can cause substantial difficulties for financing the manufacturing.
3. There are leaks in the packaging
The low quality of hand-made packaging in India results in package leakage because of financial constraints. It has always been difficult to use high-tech gear due to the high cost.
4. There are many competitors
The spice sector is highly competitive because there are so many vendors. Rivalry primarily occurs at the regional level. In addition to the many small local businesses, there are also numerous organic spices that have grown in demand because of strict quality standards.
5. Spices wastage at handling level
At every stage of handling of spices, be it for cleaning, storage, processing or packaging, there is wastage due to improper handling of the powders. This ultimately contributes to loss in profit for the manufacturer. Automation systems to avoid this are not available at all sites.
Steps followed by the current industries for manufacturing spices:
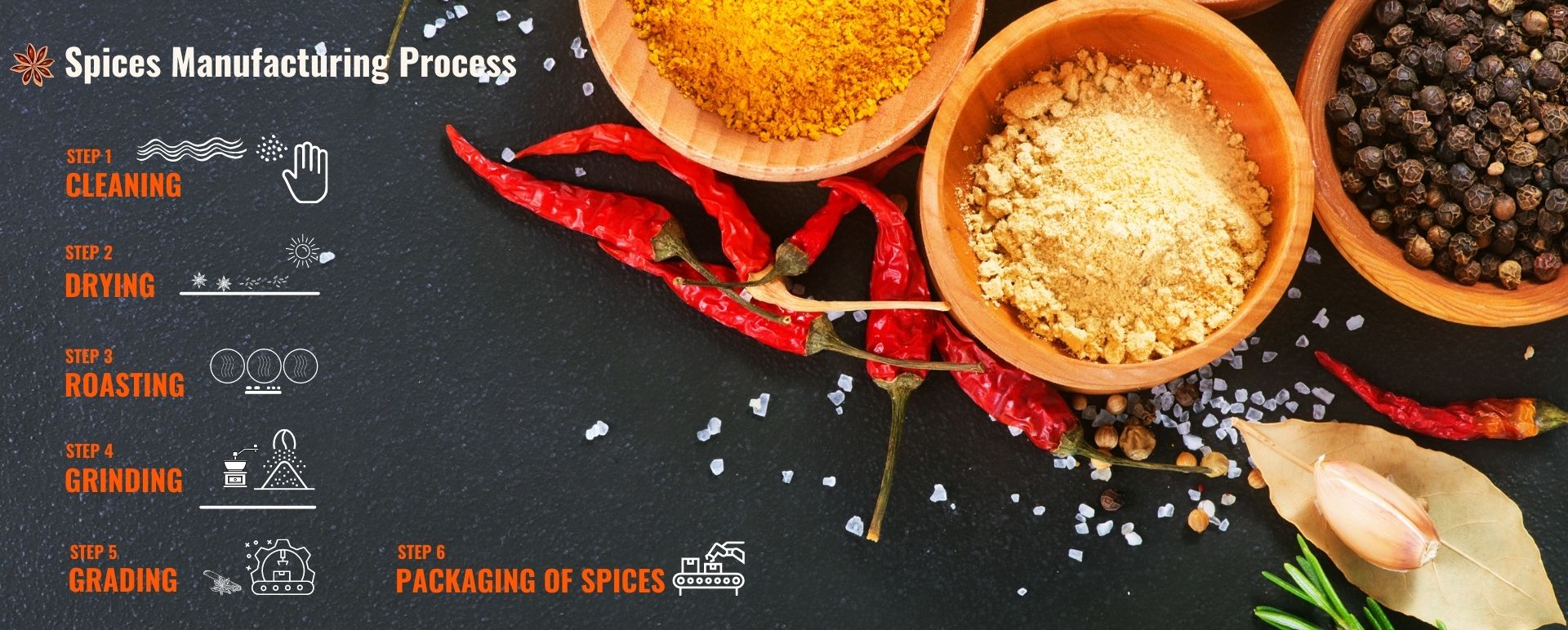
Procurement of spices:
Spices grown on Indian fields provide the finest perfume and flavour. It is of paramount essence that the quality control process for us begin on the fields (at the production centres). When it comes to producing high-quality spices, drying is an important step. The results of the other phases in the manufacturing process are greatly influenced by the level of perfection achieved during the drying process. Proper drying is key to keeping the fragrance and flavour of the material. The material is naturally dried by sunlight but roasted if needed to maintain optimum moisture content.
All bulk seeds are gathered in a warehouse and mass dried before being delivered to various places in small and jumbo bags, depending on the needs. A seed is often packaged in 25 kg bags, 625 kg bulk bags, or 1000 kg jumbo bag. To preserve quality, proper transportation is required. It’s critical to have the correct supply chain in place.
Cleaning of dried spices:
Before processing, the crop should be cleaned. The first step is to use a winnowing basket to eliminate dust and grime. Bamboo, palm, or other leaves can be used to make this. Someone who is used to this type of labour can swiftly and effectively remove the dust, grime, and stones. Contaminants are removed from spices and herbs by washing them with weak alkaline cleaning solutions and neutralising agents, then passing them through concentric zones with counter-current flow, spray rinsing, and drying.
Clean and dry material is kept in an intermediate storage silo, a tank, or a hopper near the process area, and the stored material is pneumatically delivered to the grinding machine for further processing. A variety of pneumatic conveying systems can be used depending on the material to be treated, its qualities, and the desired output.
Grinding post-cleaning:
In the regular grinding of spices, energy is used to fracture the large particles into smaller ones while maintaining product quality in terms of flavour and colour. Heat is produced in this process as energy is used to fracture the small particles into smaller ones.
Grinding the spices is done using either low temperature or cryogenic methods. Using cold air in the first situation and liquid nitrogen in the second, heat is controlled within safe limits in the grinding chamber and throughout the milling system. In this way, the final spice powders are more fragrant, colored, and flavourful.
Spices are crushed using horizontal and vertical hammer mills, as well as roller mills, to decrease the size of the material to the desired size. Coarse and fine particle materials are pneumatically handled after grinding and sent to the mixing process, where all elements are blended according to specifications.
Mixing:
By pneumatically connecting grinding equipment to mixers, spice powders can be compressed and mixed according to customer requirements. As with the previous process, this is likewise fully automated and requires no operator interaction. The total processing system is designed to operate continuously, even when mixing is a batch process. The finished commodities are emptied into the tiny hopper when the mixing cycle is done, and the material is pneumatically carried into the intermediate storage silo/tank.
Post-mixing:
If you want to store the finished spice powders efficiently and easily integrate them into consumer packaging, 25 kg bags or jumbo bags or Intermediate Bulk Containers (IBCs) are a great choice. After final mixing, selecting the appropriate automatic bagging machine for finished goods is vital to guarantee that the material given to the consumer is weighed correctly in its packing. To pick the correct bagging machine, you must first establish the sort of product for which the machine is required, the material of the packaging you wish to use, and the throughput, or the number of bags that need to be filled per minute. The final bags are then either heat sealed or stitched before being dispatched.