Basics of Dense Phase Pneumatic Conveying
Basics of Dense Phase Pneumatic Conveying
In the world of material handling, pneumatic conveying systems have become indispensable for efficiently transporting bulk materials in various industries. Dense phase pneumatic conveying represents a sophisticated and effective solution for handling challenging bulk materials. Its ability to navigate through cohesive, abrasive, and fragile materials with minimal degradation makes it a valuable asset in various industries. As technology continues to advance, the versatility and efficiency of dense phase conveying systems are expected to play an increasingly pivotal role in optimizing material handling processes across diverse industrial sectors. This blog aims to unravel the basics of dense phase pneumatic conveying, shedding light on its principles, advantages, and applications.
What is Dense Phase Conveying?
Dense phase pneumatic conveying is one of the two methods used to transport bulk materials through a pipeline using a gas (typically air) as the conveying medium. The other method being dilute phase pneumatic conveying. In dense phase conveying, the material is transported in a more concentrated, slower-moving manner compared to dilute phase conveying with a higher product to air ratio.
Types of Dense Phase Conveying System
1. Dense phase pressure type pneumatic conveying
In dense phase pressure conveying, the dry bulk material is initially loaded into a pressure vessel. When the vessel is filled completely, compressed air is used to move the material into the conveying line. Once the vessel and the line are empty, then compressed air is switched off and the vessel is refilled for the cycle to begin again.
Dense phase pressure type pneumatic conveying is most suitable for conveying fragile or abrasive materials.
2. Dense phase vacuum type pneumatic conveying
This system is typically used to transfer granules and powders for short distance applications. This system features a vacuum vessel used to create batch type suction cycles to transfer material into the vessel. Once the vessel is full of material, the discharge valve opens, releases the transferred material and the vessel is taken into vacuum once again for the cycle to restart.
This type of conveying is also widely known as powder transfer system.
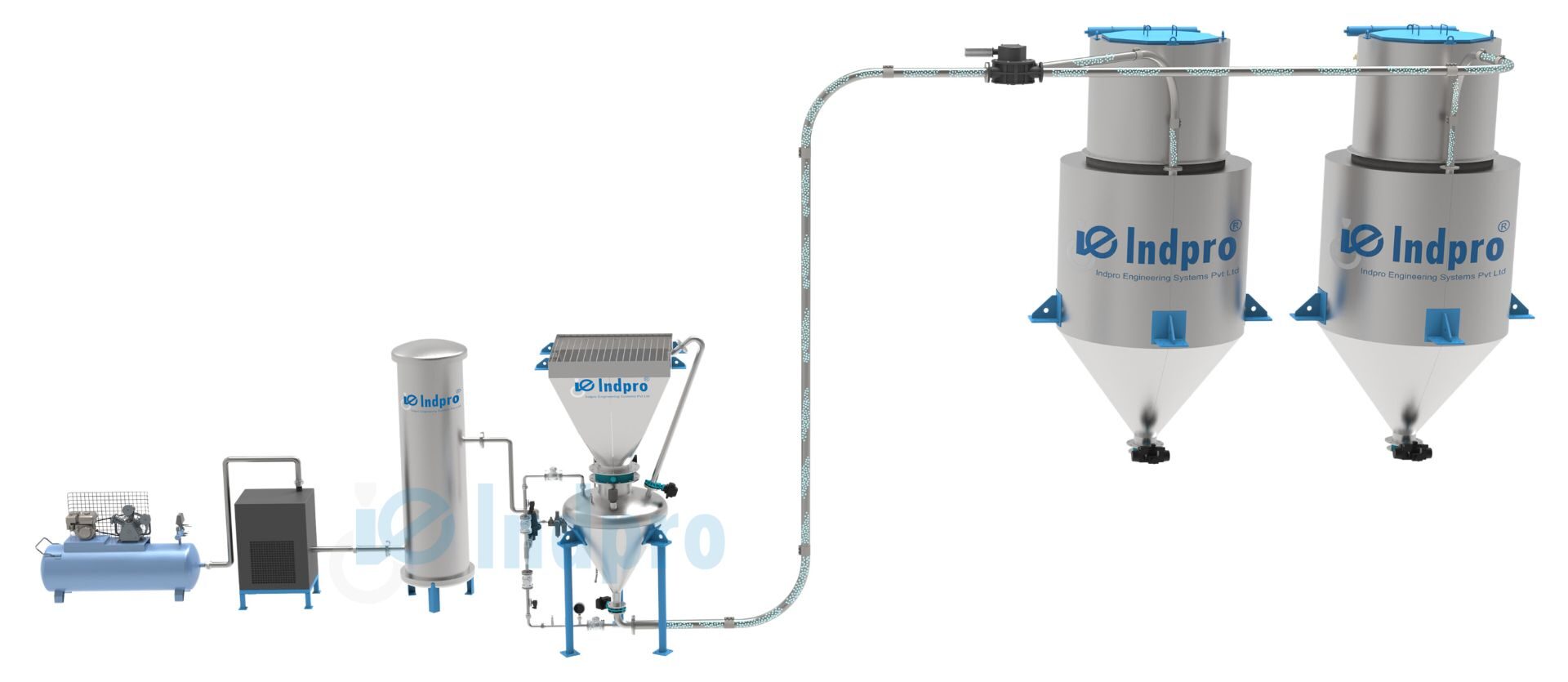
Working Principle of Dense Phase Conveying System
Here is a general overview of the working principle of a dense phase conveying system:
Material Filling:
The process begins with the filling of a pressure vessel with a batch of bulk material. The pressure vessel is sealed to create an enclosed system.
Pressurization:
Positive pressure is applied to the pressure vessel using a pressure source, such as a positive displacement blower or compressor. This pressurizes the air within the vessel.
Material Fluidization:
The pressurized air fluidizes the bulk material, creating an aerated mass within the pressure vessel.
Material Injection
The material is then injected into the conveying pipeline. The discharge device ensures uniform plug or slug formation of material as it is injected into the pipeline.
Conveying:
Pipeline conveying occurs when there is a pressure differential between the pressure vessel and the pipeline, which causes the dense material to plug to move through the pipeline. This movement takes place in a controlled manner and occurs at lower velocities compared to dilute phase conveying.
Pressure Release:
When the material arrives at the end of the pipeline or its destination, the pressure is released, allowing the material to settle into the receiver.
Recovery and Discharge:
The recovered material is discharged from the system, either for further processing, storage, or other applications.
Key Points to Note:
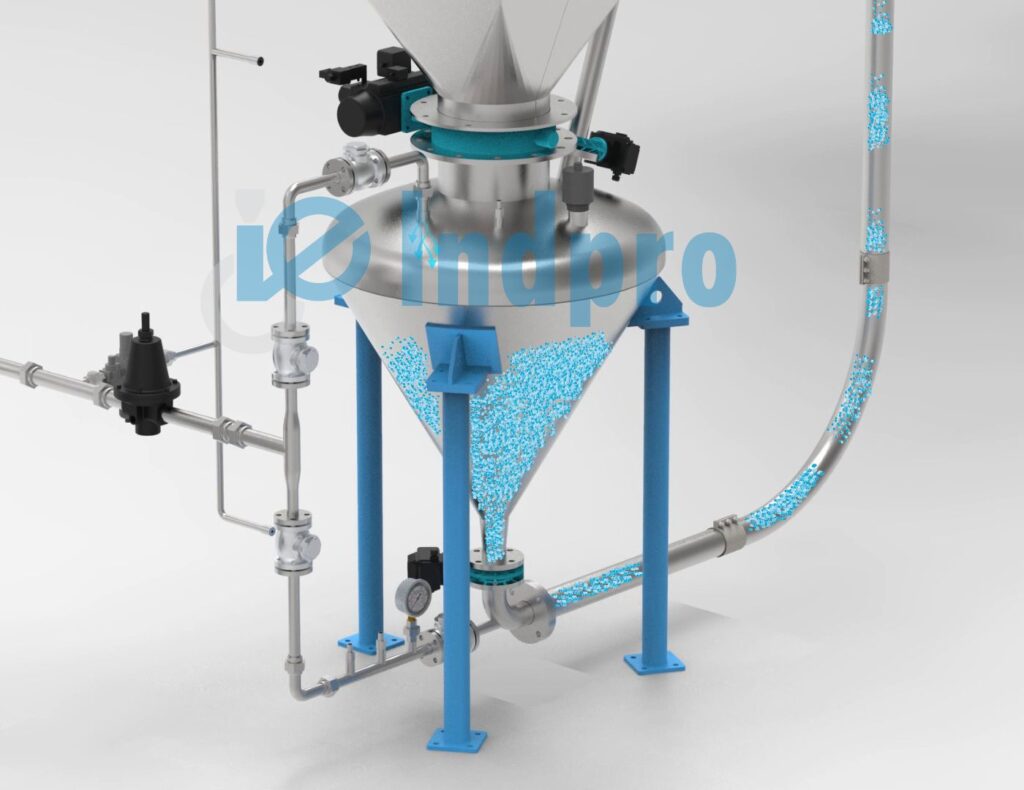
Batch Operation
Dense phase conveying systems often operate in a batch mode, where a specific quantity of material is pressurized and conveyed at a time.
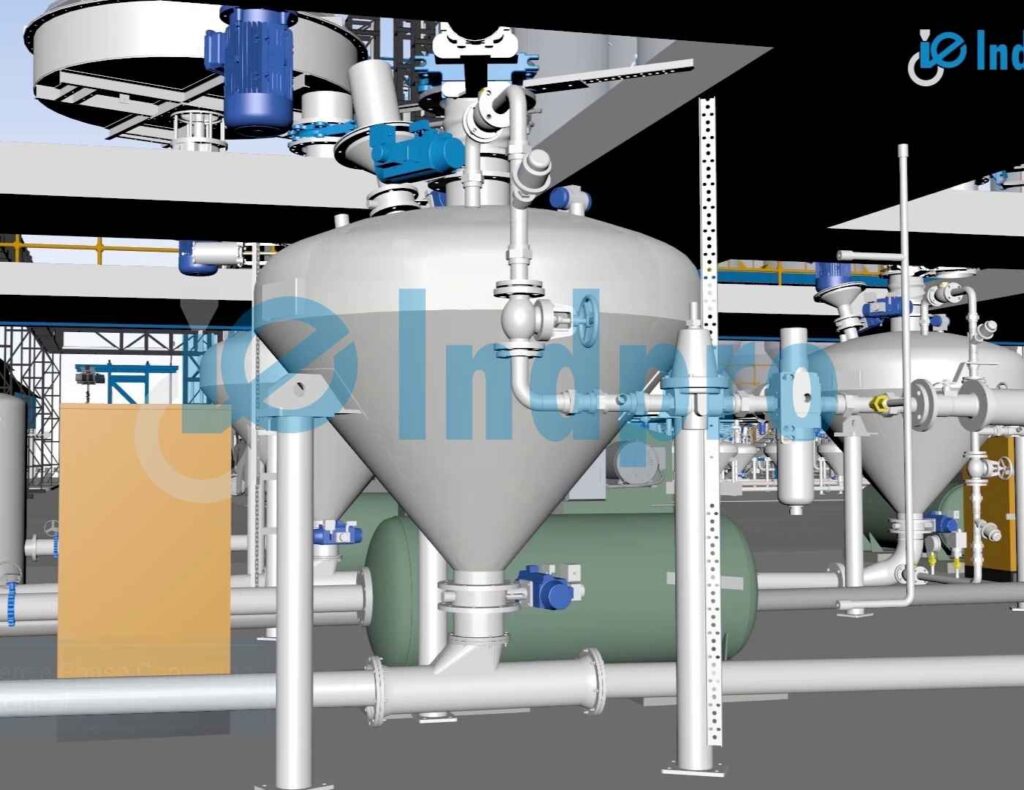
Controlled and Gentle Conveying
The system is designed to convey materials in a controlled and gentle manner, making it suitable for fragile or abrasive materials.
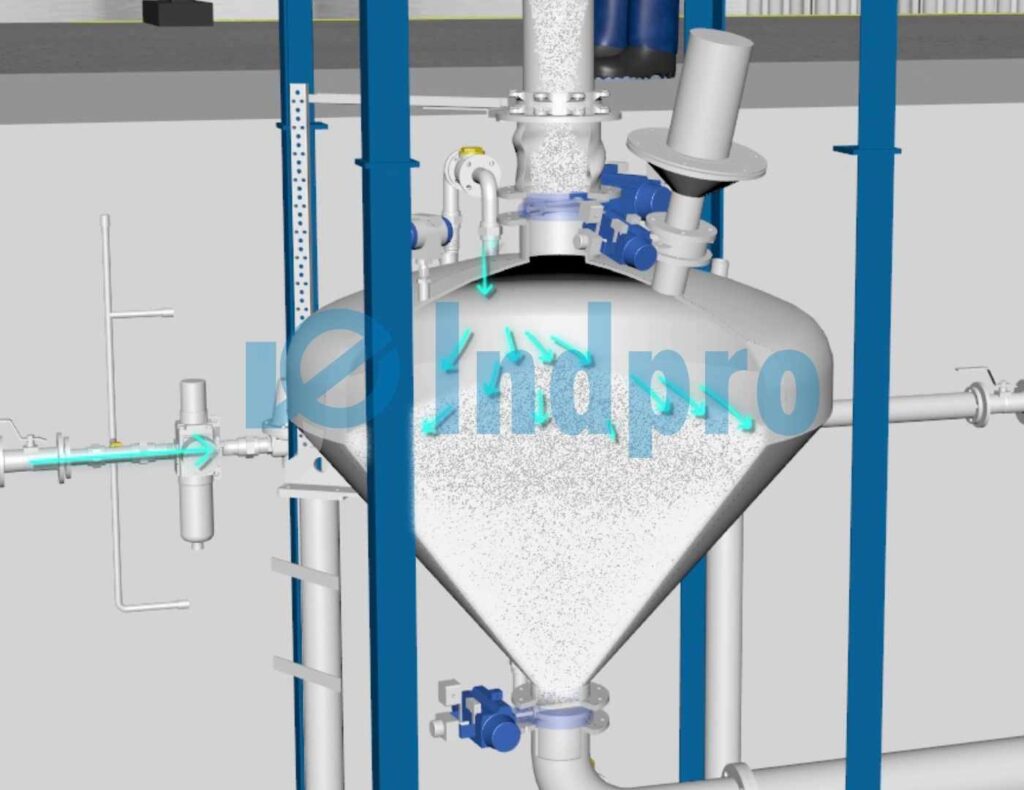
Pressure Regulation
The pressure within the system is carefully regulated to ensure the controlled movement of the material through the pipeline.
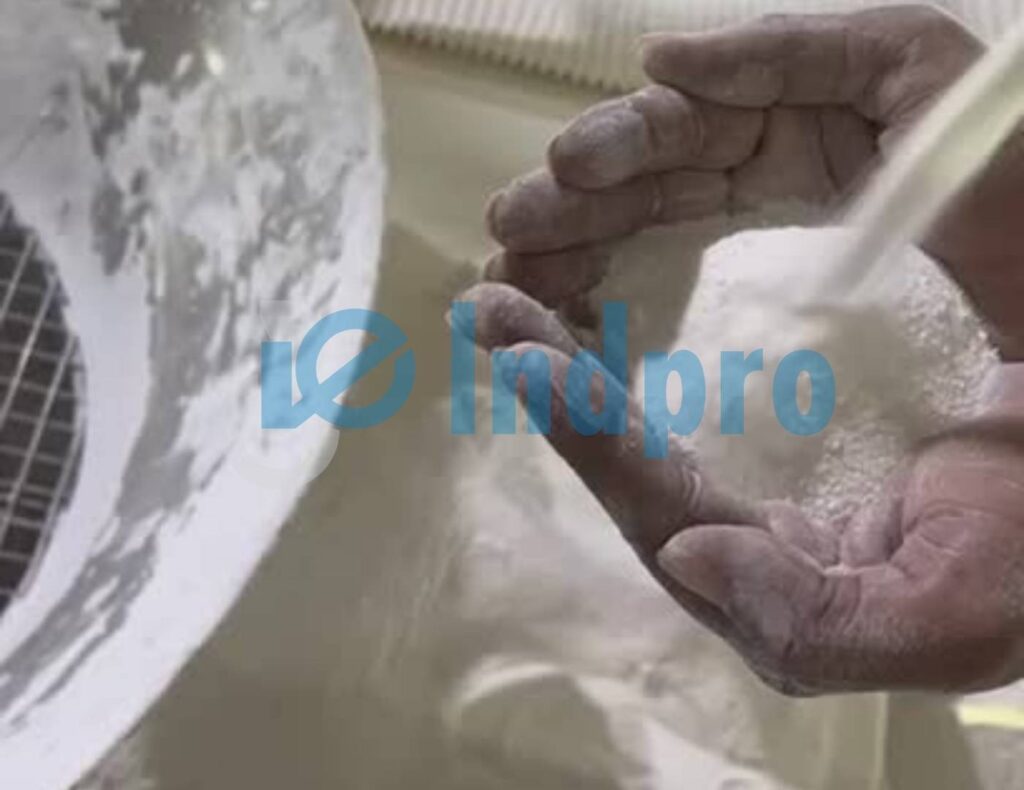
Material Integrity
The dense phase conveying process is conducive to maintaining the integrity of the conveyed material, minimizing degradation and breakage.
The working principle of dense phase conveying systems may vary based on specific system configurations, the type of pressure vessel used, and the characteristics of the conveyed material. Overall, dense phase conveying offers an effective and gentle method for transporting a wide range of bulk materials in various industries.
Components of a Dense Phase Pressure Type Pneumatic Conveying System
Pressure Vessel:
- A pressure vessel is a key component of dense phase pressure conveying systems. It is a sealed container designed to withstand high pressures up to 10 bar(g).
- The pressure vessel is filled with a batch of bulk material, and then pressurized air is introduced to create a plug or slug of material for conveying.
Batch Operation:
- Dense phase pressure conveying systems often operate in a batch mode, where a discrete quantity of material is pressurized and conveyed through the pipeline as a slug or plug.
- The batch operation allows for precise control over the material flow and pressure conditions.
Pressure Source:
- Positive displacement blowers or compressors create positive pressure along with the required flow rate.
- The pressure source pressurizes the air within the pressure vessel to create the necessary force for conveying the material.
Pressure Regulating Equipment:
- To control the conveying pressure and optimize the conveying conditions, pressure regulating equipment may be used.
- This equipment ensures that the pressure remains within the desired range for effective and controlled material transport.
Conveying Pipeline:
- The conveying pipeline is designed to withstand the pressures associated with dense phase conveying.
- The pipeline is equipped with necessary bends, elbows, and other components to guide the material through the system.
Material Receiver:
- At the end of the conveying pipeline, the material is separated from the conveying air in a designated receiver.
- Cyclones, filters, or other separation devices are commonly used to recover the material at the destination point.
Control System:
- A control system is employed to regulate and monitor the pressure, air flow, and other parameters throughout the conveying process.
- The control system ensures that the conveying system operates efficiently and within the desired parameters.
Materials conveyed by Dense Phase Pneumatic Conveying
- Alumina
- Dolomite
- Feldspar
- Silica sand
- Carbon black
- Fly ash
- Glass batch mix
- Hazelnuts
- Puffed rice cereal
- Cocoa beans
- Dextrose
- Sorbitol
Advantages of Dense Phase Conveying:
- Reduced material degradation: Gentle material handling minimizes the risk of particle breakage or attrition.
- Lower air consumption: Dense phase systems generally require less air volume, leading to energy savings.
- Minimal wear and maintenance: The controlled, low-velocity movement reduces wear on the pipeline and components, contributing to longer equipment lifespan.
- Suitable for long distances and vertical lifts: Dense phase conveying can effectively transport materials over extended distances and handle vertical conveying challenges.
Applications of Dense Phase Conveying
Dense phase pneumatic conveying finds application in a variety of industries, including:
1. Chemical processing
2. Food and beverage
3. Pharmaceutical manufacturing
5. Minerals and mining
High-quality fabrication is crucial for the success of pneumatic conveying systems. It ensures efficient material flow, durability and longevity, and the safety of workers and the surrounding environment. By using advanced techniques such as metal shaping, welding, and finishing, and working with a skilled fabrication team, you can ensure that your pneumatic conveying system is built to the highest standards and will provide reliable and efficient performance for years to come.