Types of valves used in pneumatic conveying systems
Types of valves used in
pneumatic conveying systems
Valves play a crucial role across various industries, serving to control the flow of gas and fluid through specific connection lines. With diverse types and functions, valves aid in redirecting or restricting the flow of substances within a system.
Industrial valves are designed to regulate, start, change, separate, or stop the flow of fluid or gas in a set direction. Besides that, they can also help ease excessive pressure from different vessels or systems.
There’s a whole variety of valve types for all wide range of applications. If you’re dealing with industrial setups that use valves for different reasons, understanding the various types is key. Let’s check out the different kinds of industrial valves!
Type of valves used in Pneumatic Conveying System
1. Butterfly Valve:
A butterfly valve is a quarter-turn valve used to control fluid flow in a pipeline. It’s called “butterfly” because the disc inside looks like a butterfly’s wings when it rotates. This disc sits in the middle of the pipe and when turned 90 degrees, it either allows or blocks the fluid flow. These valves are great for isolating vessels or in pneumatic conveying pipelines for handling bulk solids.
Butterfly valves are differentiated in terms of type of construction in the following ways:
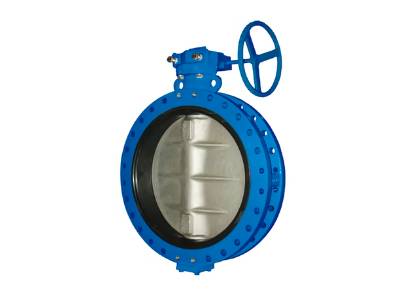
Concentric Butterfly Valve
It is the most common type of butterfly valve the where, the shaft which connects the actuator to the disc of butterfly valve known as ‘stem’ is positioned at the center of the disc.
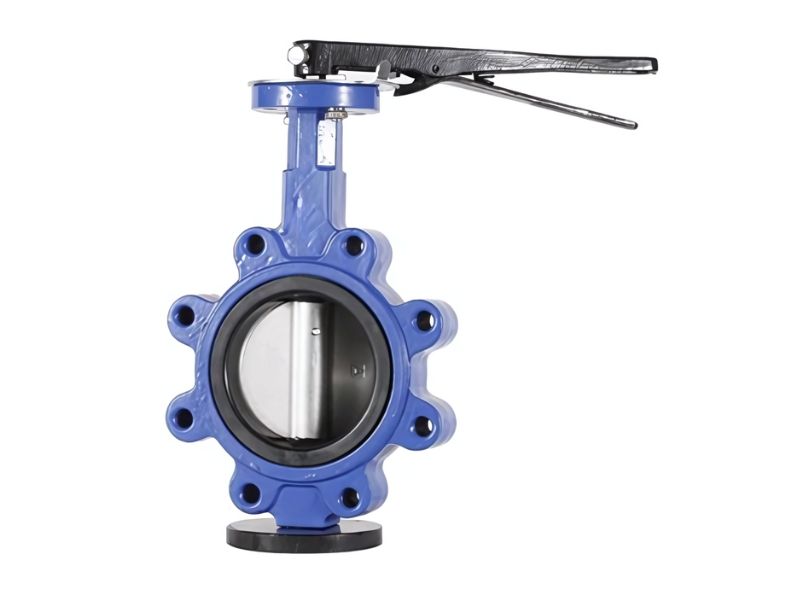
Lug-style Butterfly Valve
This valve has threaded inserts at both sides of the valve body. The valve is mounted between two flanges.
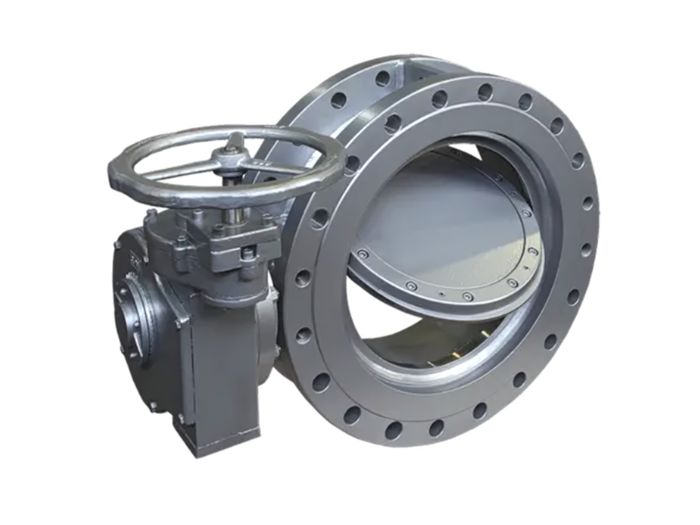
Eccentric Butterfly Valve
The stem of this valve is located off-center, which allows for a more resilient seating arrangement. There are two types: high-performance valves and triple offset valves. High-performance eccentric valves have a slightly offset stem, while triple offset valves have a more pronounced offset.
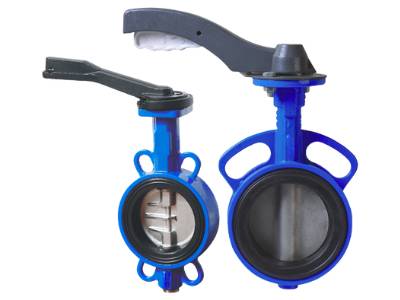
Wafer-style Butterfly Valve
This valve is designed to fit between two flanges without the need for bolts and nuts through the flange holes, typically 4 in number. It is held in place by the flanges.
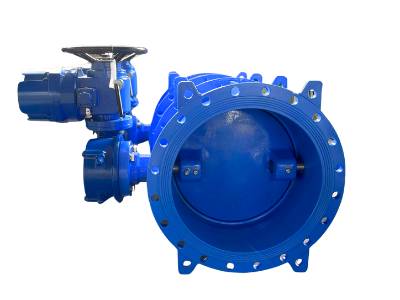
Flanged Butterfly Valve
This valve is installed between two flanges using bolts and nuts to secure it in place. It is suitable for applications where the pipeline has flanges at both ends.
Butterfly valves are widely used in various industries due to their simplicity, lightweight design, and relatively low cost. They are suitable for applications where tight shut-off is not critical, and a quick quarter-turn operation is desirable.
2. Knife Gate Valve:
A knife gate valve is a special type designed to cut through thick fluids using an edge blade. These valves are commonly used when you need straight-line fluid flow with minimal restrictions. They’re also used for isolating vessels or feeders handling bulk solids. They are typically designed for heavy loads.
The main types of knife gate valves used are:
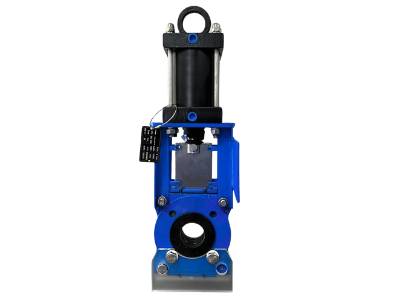
Slurry Knife Gate Valve
Specifically designed to handle abrasive and viscous slurry fluids. The gate is designed to cut through the slurry without causing excessive wear.
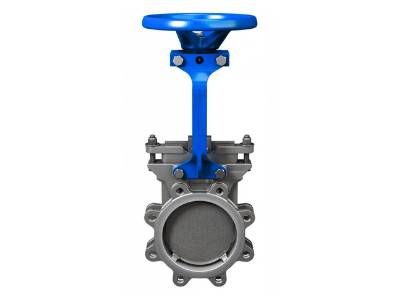
Uni-Directional Knife Gate Valve
Flow is restricted in one direction only. This type is suitable for applications where a one-way flow is desired.
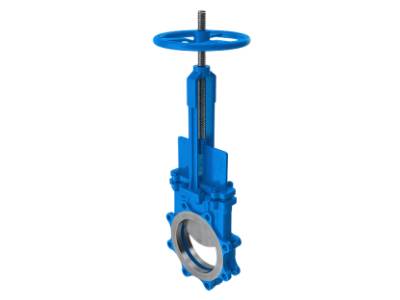
Bi-Directional Knife Gate Valve
Flow can occur in both directions. It provides versatility in applications where fluid flow may need to change directions.
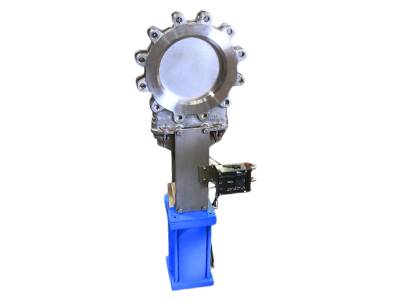
Lug-Style Knife Gate Valve:
Like lug-style butterfly valves, these valves have threaded inserts at both sides of the valve body. Typically used in applications where the valve is positioned between two flanges.

Wafer-Style Knife Gate Valve
This valve is designed to fit between two flanges without the need for bolts and nuts through the flange holes, typically 4 in number.
3. Ball Valve:
Ball valves have a design with a big sphere and central hole for smooth fluid flow. They’re great at controlling high-pressure liquids and gases while reducing pressure drop. Their quick response time makes them efficient for fast opening and closing actions. Ball valves are versatile and perfect for different pneumatic conveying system applications. Here are some common types of ball valves used in pneumatic conveying:
The main types of ball valves used are:
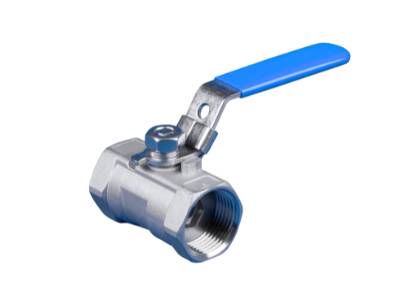
Two-way (shut-off) ball valve
controls the flow of air or gas in a straight-through path. It allows the system to start and stop as needed.
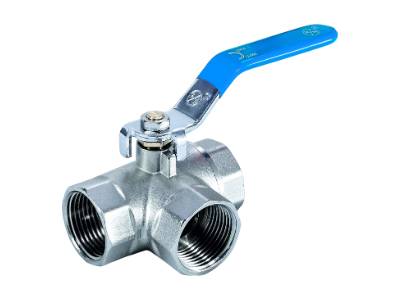
Three-Way (Diverter) Ball Valve
These valves have three ports and can redirect the flow of air or material between two different paths. Used for diverting air flow to different destinations within the pneumatic conveying system.
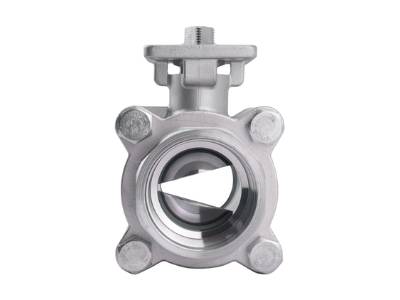
V-Port Ball Valve
These valves have a V-shaped port in the ball, allowing for more precise control of flow by partially opening or closing the valve. Used in applications where throttling or modulating the flow is required.
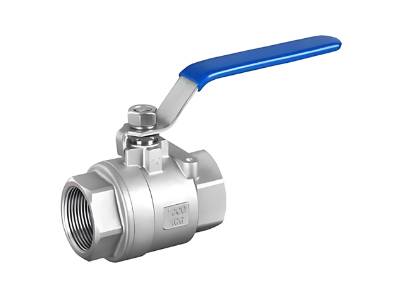
Full-Port Ball Valve
These valves have a larger port size, providing minimal restriction to flow and reducing pressure drop. Suitable for applications where maximizing flow capacity is important.
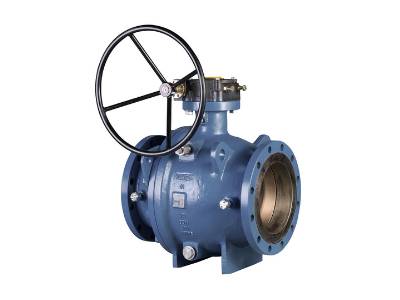
Trunnion-Mounted Ball Valve
provides additional support for the ball , ensuring stability and reducing pressure on it . Used in high-pressure pneumatic conveying systems.
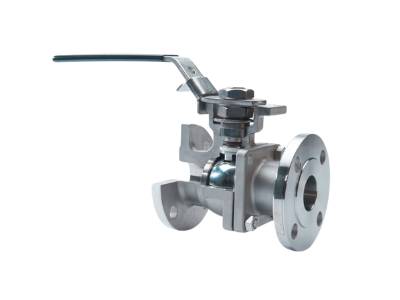
Metal-Seated Ball Valve
These valves have metal seats, providing better wear resistance and durability, especially in applications with abrasive materials. Suitable for handling abrasive materials in pneumatic conveying systems.
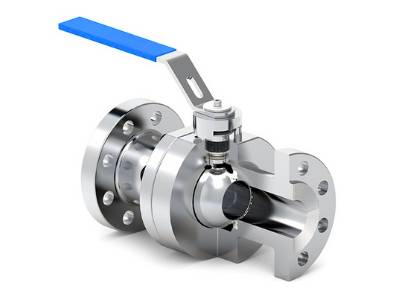
Floating Ball Valve
The ball in these valves is not fixed and can move slightly to ensure a tight seal against the seats. Used in applications where a tight seal is crucial to prevent leakage.
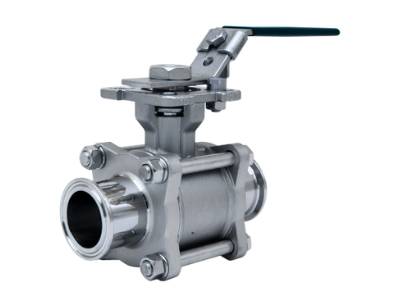
Cavity Filled Ball Valve
These valves have a cavity filled with a sealing material to enhance sealing performance. Suitable for applications requiring enhanced sealing in pneumatic conveying.
Butterfly, ball and knife gate valves can be operated using various methods, including manually, electrically, pneumatically, or hydraulically. The choice of actuation method depends on the specific application requirements and the preferences of the system designer. These valves are commonly actuated by the following methods:
1. Manual Operation:
Handwheels or levers are used to manually turn the stem and control the position of the disc or gate.
2. Pneumatic Operation:
Compressed air is used to actuate the valve. Pneumatic actuators are common for these valves, especially in applications where quick and efficient operation is needed.
3. Hydraulic Operation:
Hydraulic systems use fluid pressure to actuate the valve. Hydraulic actuators provide more force and are suitable for larger valves or applications with higher operating pressures.
4. Electric Operation:
Electric motors drive the valve’s actuator. Electrically operated valves are suitable for applications where continuous modulation of the valve position is required.
The choice between hydraulic, pneumatic, or electric actuation depends on factors such as the size of the valve, the required operating pressure, the speed of operation, and the automation level desired for the system. In many cases, pneumatic actuation is a popular choice for these valves due to its simplicity, cost-effectiveness, and the ability to provide rapid on/off control.
4. Diverter Valve:
Diverter valves are classified based on their diverter mechanism and application. Three common types of diverter valves are:
This type finds its application for flow of bulk solids due to gravity, facilitating diversion to multiple destinations, in a vertical format. It is ideal for scenarios where the movement of bulk solids needs to be directed to various receiving points. These are typically operated using a pneumatic actuator.
Primarily used in pneumatic conveying systems and bulk solids handling applications of powder or granular material to redirect the flow from a single inlet to two separate outlets or vice versa. The versatility allows this unit to be mounted in any direction, depending on the configuration of the pipeline. It diverts dense or lean phase solids conveying to various destinations without disrupting the gas flow. These can be used up to a pressure of 6 bar(g) in usual applications. These are typically operated using a pneumatic actuator.
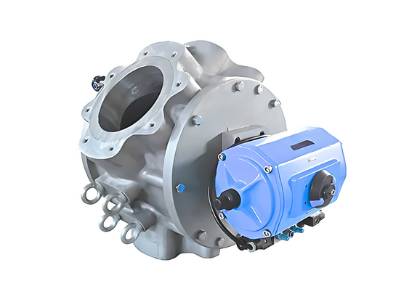
Single Tunnel Diverter Valves
Similar in application to a dual tunnel diverter valve, however instead of having 2 tunnels on the inside, this unit consists of just 1 tunnel. For larger sizes, this design is better suited since it is more compact and easier to maintain.
5. Non-Return Valve:
Non-return valves, also known as check valves, are essential in pneumatic conveying systems to allow one-way flow of air while preventing backflow of either air or material. Common types include swing check valves, lift check valves, spring-loaded check valves, in-line check valves, diaphragm check valves, disc check valves, wafer check valves, and dual-plate check valves. Their selection depends on factors like material type, system pressure, and application orientation. These valves play a crucial role in maintaining system efficiency and preventing issues such as material contamination and equipment damage.
6. Pressure Regulating Valve:
In pressure regulating valves, high-pressure fluid or gas initiates the process. A spring within the valve exerts a consistent force to slightly open it. This allows the fluid or gas to flow through, filling the outlet end. As the outlet pressure builds, it pushes the valve upward, closing it. Essential in industrial processing, water distribution, and steam systems dealing with high pressure.
Pressure regulating valves in pneumatic conveying systems control and maintain a consistent pressure of conveying air or gas. They come in direct-acting and pilot-operated types, with an adjustment mechanism for setting desired pressure levels. These valves prevent over pressurization, contribute to system efficiency, and can be integrated into control systems for automated adjustments. Proper selection, installation, and maintenance is crucial for reliable pneumatic conveying performance.
7. Pressure Relief Valve:
Pressure relief valves in pneumatic conveying systems automatically release excess pressure to prevent over pressurization, safeguarding equipment from damage. They come in direct-acting and pilot-operated types, with a set pressure point for activation. These valves serve as safety features, protecting pipelines and components. Some models reset automatically, while others may require manual intervention. Compliance with safety standards and regular maintenance is crucial for their effective operation in pneumatic conveying applications.
8. Solenoid Valve
Solenoid valves are essential in pneumatic conveying systems for controlling the flow of air or gas. They operate electromechanically, responding to electrical signals to open or close. Types include Normally Closed (NC), Normally Open (NO), Three-Way, and Four-Way valves. They play roles in diverting airflow and integrating with control systems. Solenoid valves are chosen based on pressure ratings, material compatibility, voltage requirements, and response times, contributing to the efficiency and automation of pneumatic conveying systems. Regular maintenance is crucial for their reliable operation.