Next-Gen Technology in Mechanical Material Handling
Next Gen. Technology in Mechanical Material Handling
Everyone has rules of thumb when it comes to choosing a conveying system — rules based on bulk material characteristics, required flow rates and distances, sources and destinations, plant configurations and other variables. But those with experience in all types of systems will understand that the only rule for choosing a conveying technology is that there are no hard-and-fast rules. The fact is, most materials can be conveyed using any of several methods, but which is your best choice? Leave that to the experts to guide you.
There are primarily two types of Conveying System, Pneumatic Conveying System and Mechanical Conveying System.
Pneumatic conveying is by far the most hygienic conveying method for bulk dry powders and granular bulk materials because it’s a totally enclosed system that protects materials from air, dirt, and waste, and in turn, facilities from fugitive dust. Pneumatic conveying uses gas (usually air) to transfer suspended material through tubes. A pneumatic conveyor requires a prime mover to displace air which in turn moves the material.
Mechanical conveying include tube chain conveyors, conveyor belts, aero mechanical conveyors, flexible screw conveyor, and bucket elevators that use a mechanical device which is in direct contact with the material to be transferred. The advantage of a mechanical conveyor is the ability to move large amounts of material with minimal energy consumption and minimal particle breakage.
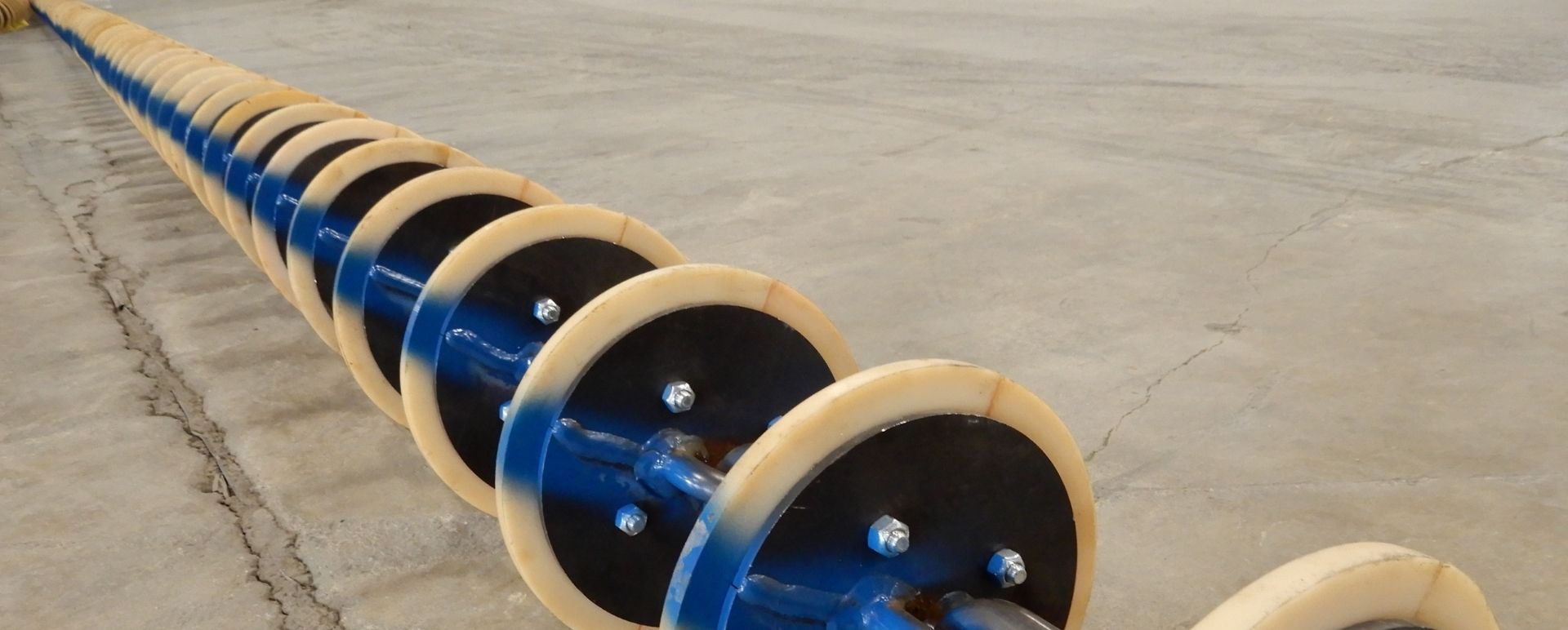
The very versatile nature of the tube chain conveyor makes it adaptable to any configuration and provides it the power to handle all kinds of bulk solids. Just about any industry that needs to convey material gently and quickly can speed up their process by integrating tube chain conveyor into their setup. One of such well known tube chain conveyors in the market goes by the name of Diskcon. Diskcon is mostly used where gentle material handling is required for fragile and perishable products. They are widely used where space is constrained. In process industries flexible material handling solutions are a need of the hour, especially in brown field project, which is where such tube chain conveyors are used.
Food industries use it to gently convey cereals, grains, coffee, peanuts, almonds as well as small-sized solids such as sugar, pepper, etc. Pharmaceutical and chemical industries use it to convey explosive powders with low minimum ignition energy. The plastic and polymer industries use it to convey polymer powders which are again explosive in nature.
Diskcon is a fully enclosed mechanical conveying system that consists of a tubular case through which the product is conveyed. Material is pulled along the channel through specially designed polymer disks with exceptional compressive strength and low coefficient of friction. Inside is a chain disk assembly which carries the material. This may be used to convey several types of bulk solids, however abrasive, hazardous, or sticky they may be. Our tube chain conveyor system can transfer almost any material gently and securely, without altering the product’s integrity.
Our tailor-made tube chain conveyor systems are used in chemical, pharmaceutical, food, polymer, and other process industries for a wide range of applications. With special versatile technological approaches, we care for individual customer requirements. Tube Chain Conveyor is an innovative concept which addresses three major industrial factors: Energy, Space & Environment. This is a gentle moving machine backed up by a control panel featuring Electronic Logic Controllers and sensors for automated operation of a chain tensioning system and an under-speed monitor, making this equipment practically maintenance-free.
A broad variety of products can be conveyed which includes food stuff, cereals, chemicals, pesticides, animal feeds, salt, sugar, dairy powders, plastics and polymers. Operating temperatures can be up to 200° C. Particles ranging from fines to 20 mm lump size, can be easily conveyed. This conveyor comes in stainless steel constructions, with the conveyor chain made from hardened and tempered steel alloy materials, with high tensile properties and wear-resistant.
The heart of our system lies in the driving station, which gives the chain-disk assembly the necessary force for gentle conveying.
DiskCon’s chain tension station continuously tensions the whole chain length in the conveying direction of the equipment while maintaining minimal tension in the return route. It helps reduce chain-disk mounting, sprocket, valve and pipe.
Every bulk solid has different physical and chemical properties. The sum of cohesive and elastic power that it produces defines its flow behavior and pattern.
When compared to a rope, the chain is less susceptible to exhaustion, tear, and elongation. Individual disks can be substituted in a tube chain conveyor in the event of any unexpected damages and may be substituted completely in the case of cable conveyors. Diskcon’s UHMWPE disks are lightweight, have excellent compression properties, and have a high resistance to wear coupled with low friction. Each of these properties offers optimal conveying for reduced energy usage, with small power requirements.
Cohesive and sticky bulk solids require separating cleaning devices from the chain-disk assembly. This is where the brushes mounted inside the driving station ensure that minimal material residue is left over the chain disk assembly while it returns.
We use specialized conveyor tubes that have extremely accurate dimensions and low resistance to movement. Standard ERW tubes cause excessive wear to conveyor disks. Due to a smooth inner finish, our conveyor tubes have low friction, which helps to minimize power consumption and disk wear. The conveying tubes are built for high tensile strength which requires minimal external supports.
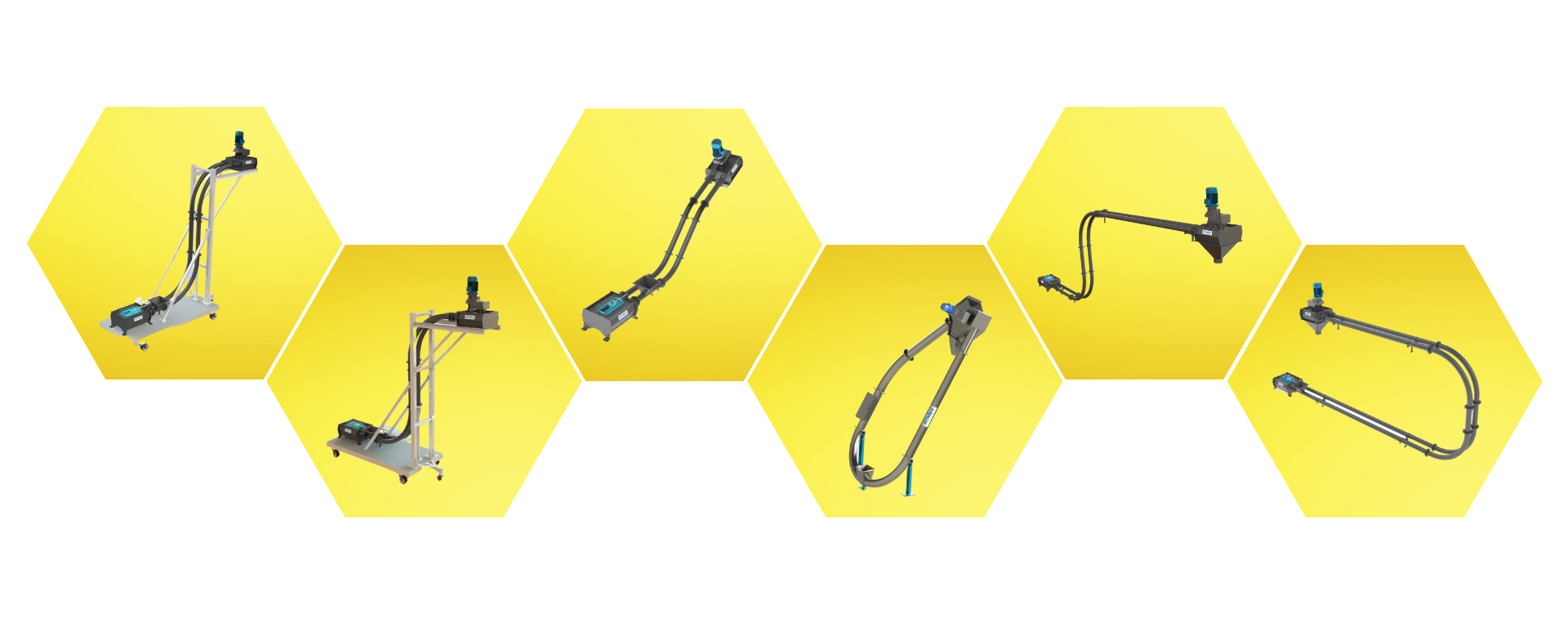
Our conveyor uses a chain rather than a cable, which is why they can be run anywhere between 0 and 100% load.
The quality of the bulk material is entirely protected, which means you receive the same material from the outlet like the one you put in the inlet.
The chain tensioning station constantly tensions the whole chain length in the conveying direction of the commodity while maintaining minimal tension in the return route to minimize wear.
The very flexible design of the Diskcon helps it to conform to any setup and enables it to accommodate all types of bulk solids. Just about any industry that needs to gently and quickly convey material can speed up its process by integrating Diskcon into its setup.
Tube chain conveyors consume less than half the power for the same distance and capacity compared with our pneumatic conveying system.
We individually plan your system in a modular design. Layout, materials, and speed will be perfectly adapted to your bulk material.
We also supply several accessories, such as a cleaner assembly or air spray to clean the chain disk assembly on the return line, manual or pneumatic slide gate valves to monitor product discharge.
Diskcon is the ideal solution to handle fragile, explosive, and hygroscopic bulk solids.
Material is gently handled inside the tubing at a very low intensity.
Due to its compact dimensions, low maintenance, ease of use, and amazingly low energy consumption, this system operation is completely free from dust.
After years of material handling experience, and having experienced a variety of bulk solids, we provide material feeding devices that are best suited to your specific needs.
Users can choose which system (speed-size combination) they require for their material from our wide range of conveyors, or we could suggest one based on our experience in handling bulk solids.
We offer the following range of tube sizes: 4″, 5″, 6″ and 8″
Indpro’s Diskcon is available in Stainless Steel construction for food & pharmaceutical applications.
We offer standard configurations: C Type, Z Type, Inline TCC, Inclined TCC, Transfer Type, O Type, Inclined O Type, and Portable Type.