Centralized de-dusting system
Dedusting system for lower emissions
A centralized dedusting system is also known as dust collectors, bag filters, or bag house. In manufacturing plants, dedusting is necessary for a safety and better working environment. As a result, selecting the right filtration system becomes crucial.
Large capacity modern plants are designed in a way that the conveying and process equipment is centralized in one area. Instead of individual multiple-point filters, a common large scale filtration system is set up to gather the dust from various sources using a network of aspiration lines. The centralized dust collector draws process air through the filter media using an outside fan before releasing it into the atmosphere. When the filter medium is being cleaned, compressed air creates a shock wave throughout the length of the element to force the dust or cake to fall off the element's exterior and back into the filter hopper.
Centralized dust collector filters gather dust from a variety of locations, including bag dump stations, big bag stations, container unloading stations, mechanical conveyors, mixers, blenders, sifters, hoppers and silos, and packing machines.
There are various filter media types to choose from depending on the application, dust characteristics, temperature,
and moisture level of the substance. The filter bags or cartridges are of removable and replaceable types.
Depending on the needs of the customer, our dust collecting system offers multiple levels of filtration, including HEPA
filters, cyclones, bag filters, and cartridge filters. Depending on the type of arrangement and application, we can
achieve emission levels as low as 5 mg/Nm3. Based on your requirements, our team can recommend the best dust
collector for your operation.
Product Features

Types of filter elements in specialized dust collectors
Related Products
There are many more products and systems which you can explore

Indpro
Typically replies within an hour
Send Enquiry
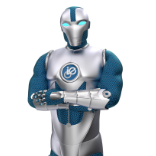