PelletPurge®
Introducing the Latest in Pellet Technology in India – PelletPurge® by Indpro.
Indpro takes immense pride in introducing a revolutionary Pellet Cleaner technology in India. Our innovative solution ensures the thorough cleaning of particulate products such as plastic pellets and granular products before storage, manufacturing, or packing. Experience enhanced quality control and supply superior materials for your downstream processes with ease.
Why Do We Get Fine Particles and Why Does Cleaning Matter?
In any industry, it's crucial for products or raw materials to be free from contaminants to ensure the quality of the final product. Granular materials like tablets, grains and pellets often pick up contaminants and generate fines during processes like mixing, blending, or transportation. As these materials move through pipes and ducts, friction between particles and the pipe walls creates dust, micro-dust particles, and streamers, which act as contaminants.
These contaminants negatively affect the final product. Therefore, it's essential to have a cleaning
system in place to remove these particles. It's also important for these cleaning systems to be positioned just
before the next manufacturing, storage or packing stage to prevent additional contamination during
transportation.
Additionally, static charge buildup in materials also attracts dust, making it challenging to remove. Therefore,
it's necessary for the cleaning system to eliminate static charge to ensure thorough dust removal.
The significance of efficiently cleaning these granules cannot be overstated. This is predominantly used in the
plastics industry
to elevate the quality of process input pellets and the final plastic products. Whether it's the food and
pharmaceutical sectors ensuring sterile conditions, or the minerals industry addressing environmental and health
concerns, the act of cleaning bulk solids plays a pivotal role.
PelletPurge® goes beyond its
application in the plastics sector. Its versatility extends to various industries including food, minerals,
pharmaceuticals, and more. It effectively cleans a wide range of dry bulk solids such as rice, corn, peanuts,
coffee beans, iron ore, specialty sand, and wood pellets.
The reasons behind bulk solids cleaning
are multi-fold. In the food and pharmaceutical sectors, hygiene is paramount, ensuring the end product meets
stringent quality standards. In the minerals industry, the emphasis is on averting environmental and health
risks. Meanwhile, the plastics industry leverages the technology to enhance both the quality of pellets and the
final plastic goods.
The inception of the PelletPurge® was driven by the demand for uncompromising
quality standards in the plastics sector. However, the technology's capabilities stretch far beyond this realm,
encompassing a wide array of granular bulk materials. Whatever your industry, if bulk solids cleaning is a
requirement, the PelletPurge® stands as the solution of choice.
How it works:
PelletPurge® operates through a series of essential steps:
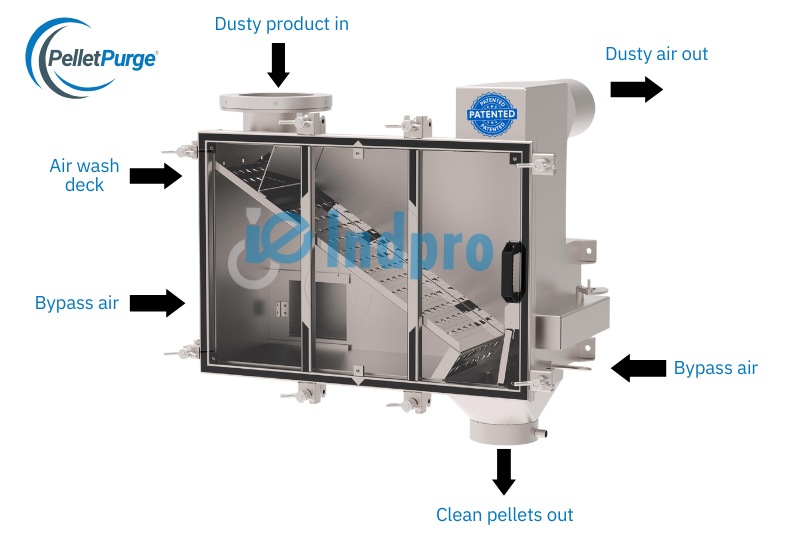
Applications
- Cleaning plastic pellets on the machine feed throat before Injection molding or extruder for best optical clarity.
- Cleaning plastic pellets as they are fed into a central surge bin or day bin that feeds several machines or dryers.
- Cleaning station in Railcar or truck unload system to remove contaminants (dust & streamers) before loading into storage silos.
- Cleaning flake in recycling plants before going through an optical sorter to eliminate dust that often blinds the camera.
- Cleaning plastic pellets as they are fed into a dryer.
- Cleaning regrinds inline or offline to eliminate dust before reprocessing for the best part quality.
- Cleaning pellets before packaging into bins or bag.
- Cleaning pellets before load out into trucks or railcar.
20+years of
Automating your bulker unloading and pellet cleaning system

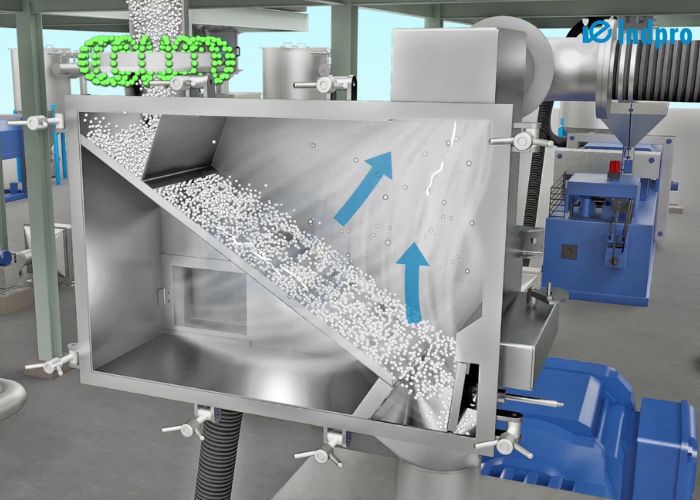
Looking for something more?
Our PelletPurge® can very well be integrated with other system solutions we offer. You can speak with our experts to know more about how we can integrate it with our Pneumatic Conveying Systems, Air Pollution Control Systems or Bulk Solids Handling Systems.
CONTACT USPelletPurge® Configuration
Open Loop System:

To prevent cross-contamination in processes with frequent product changes or lines with frequent color changes, it is recommended to utilize an open loop system. A wash air fan pushes filtered fresh air from the PelletPurge® into the cleaning air source. A secondary exhaust air fan sucks in the dusty air to a dust collector. The dusty air is separated in the dust collector and dumped into a dust container. Cleaned air is then discharged into the atmosphere.
Closed Loop System:

A closed loop system is used for routine operations with consistent product grades or for inert gas applications. The closed loop system uses a push / pull wash air fan to carry wash air into the PelletPurge®. The dust collector helps to separate the dust, and the collected dust is placed into a separate container. The purified air is then sent back to the fan to be recirculated.
Related Products
There are many more products and systems which you can explore
Latest blog post
We would love for you to know more about what goes behind designing of our systems and our considerations for the various industries we cater to.